近些年來,隨著航空事業(yè)、低溫超導、氫能源動力等領(lǐng)域的迅速發(fā)展,越來越多的裝置需要在低溫環(huán)境下運行[1–2],由此引發(fā)的潤滑問題日益嚴重。一方面,大多數(shù)液體潤滑劑在低溫下粘度增大,會逐漸失去潤滑作用,使得機械部件不得不面臨干摩擦的嚴峻困境[3];另一方面,金屬材料在低溫下發(fā)生脆韌轉(zhuǎn)變會導致機械性能急劇惡化。與此同時,在低溫下的各種嚴苛復雜的服役環(huán)境,如低溫真空、冷熱交替等更對材料的綜合性能提出了挑戰(zhàn)。
如破冰船表面材料[4]面臨著冰面物理擠壓、冰面的摩擦磨損、零下的環(huán)境溫度以及海水的腐蝕等環(huán)境因素的侵蝕。因此需要找到具備優(yōu)良的力學性能、在低溫下的抗摩擦磨損性能以及抗腐蝕能力的結(jié)構(gòu)材料以應(yīng)對復雜的服役環(huán)境。
目前對低溫金屬材料的摩擦學性能研究仍停留在較低水平,低溫摩擦領(lǐng)域的基礎(chǔ)研究十分匱乏,亟待進一步開發(fā)出能滿足低溫下具有優(yōu)異耐磨性能的金屬材料以滿足對材料日益增長的低溫耐磨需求。
1、失效方式
為開發(fā)出在低溫下具有優(yōu)異耐磨性能的金屬材料,首先需要了解低溫下材料失效的形式,這對于在低溫下耐磨金屬材料設(shè)計具有重要的科學和技術(shù)指導意義。
1.1 低溫潤滑失效
在常溫下,液體/固體潤滑是最常見的潤滑形式,但是在低溫下液體/固體潤滑劑的潤滑性能惡化,對金屬材料部件的性能提出了巨大的挑戰(zhàn)。了解低溫下潤滑劑的失效可以幫助我們更好地理解潤滑的機理。本節(jié)將從油脂潤滑劑和固體潤滑劑兩方面簡要介紹潤滑劑低溫潤滑失效的形式。
通常,油脂潤滑劑會在金屬之間形成一層油膜,通過避免金屬傳動部件之間的相互直接接觸從而達到減摩耐磨的目的。由于油脂的潤滑性能與其粘度有關(guān),隨著溫度的降低大部分油脂潤滑劑的粘度增大,流動性變差而難以發(fā)揮潤滑作用[5]。因此工作溫域較寬的固體潤滑劑成為在低溫下進行潤滑的較優(yōu)選擇。常見的固體潤滑劑有石墨、MoS2及類金剛石薄膜。石墨與MoS2獨特的層狀結(jié)構(gòu)使其層間相互作用力較低,在受力時易發(fā)生層間滑移以實現(xiàn)潤滑效果[6],但是這2種潤滑劑的環(huán)境適應(yīng)能力差,石墨晶體在真空干燥環(huán)境下摩擦力劇增[7];而MoS2在潮濕氧化環(huán)境中表現(xiàn)出高摩擦低使用壽命[8]。類金剛石薄膜雖然在潮濕環(huán)境中性能優(yōu)秀,但存在熱膨脹系數(shù)不匹配的問題[9],當溫度跨度過大時,類金剛石薄膜易于與基體之間失配,在使用過程中易于脫落、使用壽命縮短。
總之,無論是油脂潤滑還是固體潤滑,都很難滿足在超低溫下長時間服役的要求。油脂潤滑的低溫失效與固體潤滑劑的使用環(huán)境限制都無法滿足大多數(shù)低溫場景下的使用。因此低溫潤滑的失效對金屬的本征摩擦性能提出了很高的要求。
1.2 金屬材料的韌脆轉(zhuǎn)變
除了在低溫下潤滑失效之外,低溫下金屬性能的惡化同樣也對金屬的摩擦性能有著惡劣的影響。在溫度降低到一定程度時,金屬材料會發(fā)生由韌性狀態(tài)轉(zhuǎn)變?yōu)榇嘈誀顟B(tài)的現(xiàn)象,即低溫韌脆轉(zhuǎn)變。在脆韌轉(zhuǎn)化溫度之上,材料具有較好的韌性;低于臨界溫度時,則會由韌性突然轉(zhuǎn)變?yōu)榇嘈?,幾乎喪失了塑性變形能力,使金屬材料低溫下的力學性能和摩擦學性能顯著惡化。據(jù)一份描述西伯利亞雅庫特冬季采礦工具行為的報告稱:“鋼制工具變得如此脆,以至于像火柴棍一樣折斷”[10]。通常,低溫韌脆轉(zhuǎn)變出現(xiàn)在體心立方金屬、部分密排六方金屬和金屬間化合物等大多數(shù)合金體系中,面心立方金屬在極低溫時同樣存在韌脆轉(zhuǎn)變。以鋼材料為例,通過在鋼中加入鎳、錳等可使脆性轉(zhuǎn)變溫度降低,隨著含碳、磷元素的增加,脆性轉(zhuǎn)變溫度明顯升高。
低溫下潤滑劑的失效以及金屬的性能惡化導致金屬材料將面臨極端環(huán)境下干摩擦的服役環(huán)境,這使得尋找到一種可以在低溫下穩(wěn)定工作的金屬材料成為必要。目前已經(jīng)有許多學者研究不同材料以及實驗方法以獲得在低溫下耐磨的合金。常見的金屬材料有鋼材料、鋁合金、鈦 合 金 、多 主 元 合 金(multi-principal element alloy, MPEA)等。本文首先總結(jié)了常見的低溫摩擦設(shè)備,并按照不同的使用工況進行分類;隨后從不同種類的金屬材料出發(fā),詳細介紹了近期新穎的低溫耐磨材料研究成果,以期相關(guān)從業(yè)者可以快速了解該領(lǐng)域。
2、低溫摩擦實驗方法
摩擦磨損實驗的目的是研究材料在實際的工作條件下的特征與變化,揭示在摩擦過程中各種因素對性能的影響,從而確定最合適的設(shè)計參數(shù)。
摩擦現(xiàn)象的復雜性決定了繁多的實驗方法與實驗設(shè)備,因此越來越多的國家和組織開始重視實驗方法的標準化。在此基礎(chǔ)上,根據(jù)摩擦磨損的實際接觸情況和運動方式的不同,可以設(shè)計出適用于不同條件下的摩擦磨損試驗機來進行各種摩擦機理的研究。
試件之間的運動方式分為純滑動、純滾動或者伴隨滑動。試件的運動有的采用旋轉(zhuǎn)運動,有的采取往復運動。試件的接觸形式有點接觸、線接觸和面接觸。通常點接觸的單位面積壓力最大可達5000 MPa,適用于需要較高接觸應(yīng)力的實驗如膠合磨損或接觸疲勞磨損;線接觸的接觸應(yīng)力可以達到 1000~1500 MPa,適合用于粘著磨損實驗和接觸疲勞磨損實驗;面接觸的接觸壓力較低,一般為50~100 MPa,通常用于磨粒磨損實驗。當前研究廣泛采用球-盤式摩擦磨損試驗機來評估金屬材料的摩擦學性能。在實驗過程中通過施加力以及控制運動來模擬材料之間的運動,并通過控制參數(shù)來模擬不同工況,進而根據(jù)磨損率、摩擦系數(shù)等數(shù)據(jù)評估材料的耐磨性能和摩擦學特性。
對于在低溫下進行的金屬材料摩擦實驗是在以上實驗裝置的基礎(chǔ)上額外增加低溫裝置來實現(xiàn)低溫環(huán)境,從而模擬材料在極端環(huán)境下的工況,測試在不同低溫溫度下材料的摩擦學性能。當前,有關(guān)金屬材料的低溫摩擦學研究仍十分匱乏。由于低溫摩擦裝置的限制,多數(shù)研究工作的測試溫度難以低于–60 ℃。低溫裝置大多依靠低溫介質(zhì)熱傳遞來實現(xiàn),表1列出了不同環(huán)境與常見低溫介質(zhì)的溫度。本文低溫與室溫和高溫相對應(yīng),泛指零攝氏度以下溫度區(qū)間,并在不同金屬材料中篩選出近期的摩擦磨損研究研究成果進行匯報。
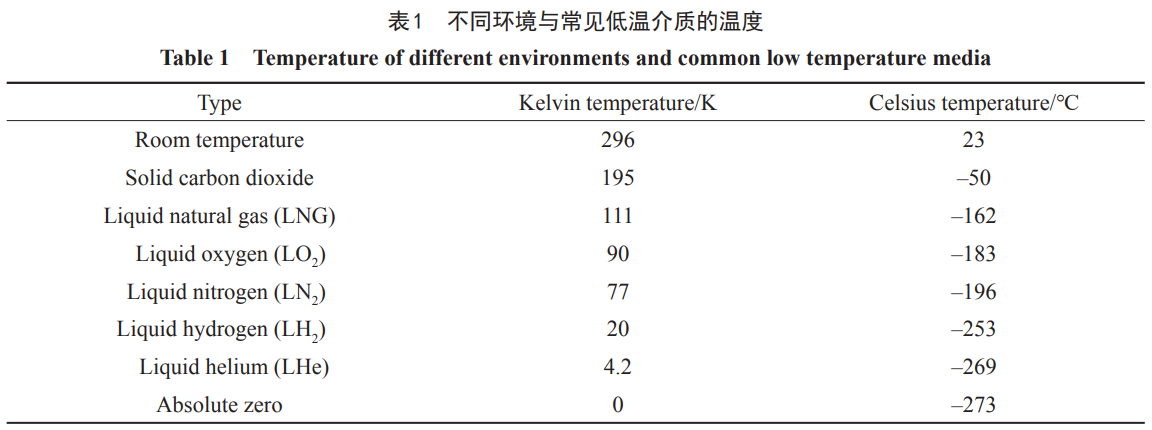
當前低溫摩擦裝置根據(jù)制冷介質(zhì)的不同可分為低溫液體介質(zhì)、低溫氣體介質(zhì)及低溫真空介質(zhì)3類,它們裝置內(nèi)部的結(jié)構(gòu)簡圖如圖1所示[11]。根據(jù)環(huán)境介質(zhì)的不同,材料的摩擦學性能也會受到相應(yīng)的影響。

2.1 低溫液體介質(zhì)
為了實現(xiàn)低溫下的摩擦學研究,通常將試樣直接浸泡在液體介質(zhì)中,即可在液體沸點的溫度下進行摩擦磨損實驗,常用的介質(zhì)有液氦、液氫、液氮、液氧等。該方法的成本較為低廉,實現(xiàn)較為簡單,但是由于摩擦熱的存在,容易在兩摩擦副之間引發(fā)液體介質(zhì)沸騰,形成蒸汽膜導致熱量傳遞的效率降低,這一現(xiàn)象在液氦之中尤為明顯。且由于液體的沸點是固定的,因此只能在孤立的溫度點進行實驗,無法對環(huán)境溫度進行較為精準的調(diào)控。
此外,由于低溫介質(zhì)與摩擦副表面會發(fā)生化學相互作用可能導致表面化學變化,這會改變材料表面相組成使摩擦實驗出現(xiàn)偏差[12]。
事實上,早在1958年就有用低溫液體作為低溫介質(zhì)進行摩擦學研究的例子。Wisander等[13]通過將填充的聚四氟乙烯組合物置于球-盤式摩擦試驗機并利用液氮浸沒將其冷卻進行摩擦學測試,發(fā)現(xiàn)其摩擦系數(shù)較低(在液氮中摩擦系數(shù)可低至0.06),同時磨損量也較小,摩擦磨損性能基本不受滑動速度的影響,與傳統(tǒng)密封組件所用的碳鋼相比有明顯優(yōu)勢。
1989 年,Iwabuchi 等[14]使用如圖 2 所示裝置分別在293、77和4 K測試了金屬與銅、不銹鋼、環(huán)氧樹脂的摩擦性能。摩擦力通過粘貼在放置于移動臂中間的圓環(huán)上的應(yīng)變片測量。77 K 下的實驗通過在每個臂上安裝試樣并加載后,將液氮倒入低溫恒溫箱中冷卻5 min,然后在液氮中開始滑動。在4 K下進行實驗時,將樣品在液氮中預冷20 min,并將液氦倒入瓶中。試樣浸入液氦5 min后開始滑動。在微動過程中,保持液氮和液氦浸沒樣品以保持溫度恒定不變。實驗揭示了在不同條件下溫度對摩擦性能的影響規(guī)律。由于低溫液體介質(zhì)的便捷可操作性較強,對實驗儀器氣密性要求較低,此后大多研究人員使用低溫液體介質(zhì)作為冷源并以此開展摩擦學研究。
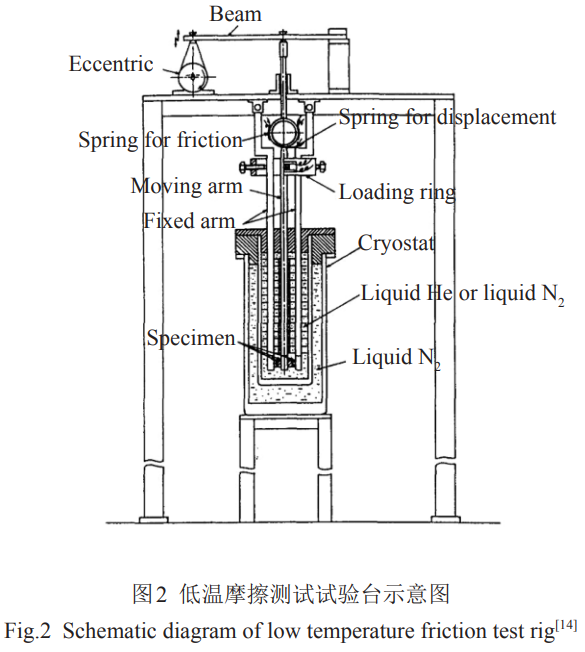
2.2 低溫氣體介質(zhì)
低溫氣體介質(zhì)方法是通過低溫氣體熱傳遞或者液體汽化的方法來降低試樣表面的溫度,通過控制氣體的流量或者噴濺液體的體積實現(xiàn)對環(huán)境溫度的控制。與低溫液體介質(zhì)相比較,低溫氣體介質(zhì)的測試溫度不再是單一的低溫液體的沸點,而是高于沸點的一定溫度范圍。同樣的,介質(zhì)的化學性質(zhì)也可能會影響摩擦副的表面狀態(tài),因此一般選取惰性氣體(如液氮、液氦)來作為傳熱介質(zhì)。
但是裝置內(nèi)部氣體交換對裝置的密封性和內(nèi)部氣氛控制提出了較高要求,否則可能產(chǎn)生諸多問題,如大氣中水蒸氣進入導致的表面結(jié)冰、氧氣進入導致的氧化以及氣氛控制不合理導致的局部溫度不均勻等。
尉成果等[15]通過低溫氮氣作為環(huán)境介質(zhì)自主研制了低溫/寬溫域關(guān)節(jié)軸承試驗機和自潤滑關(guān)節(jié)軸承。該軸承試驗機可以調(diào)節(jié)參數(shù)模擬在真實服役中可能遇到的環(huán)境,通過控制低溫軸承試驗機保溫箱內(nèi)部液氮的量來調(diào)節(jié)溫度。由此尉成果開展了113~323 K寬溫域范圍內(nèi)的摩擦磨損試驗,分析了關(guān)節(jié)軸承摩擦系數(shù)和磨損量的影響規(guī)律及機理,補全了低溫關(guān)節(jié)軸承的設(shè)計依據(jù)和摩擦系數(shù)、使用壽命等相關(guān)數(shù)據(jù),為低溫風洞中關(guān)節(jié)軸承的設(shè)計、研制和使用提供依據(jù)。
低溫氣體也會對摩擦實驗帶來溫度之外的影響。蘭州物理化學研究所的Zhu等[16]在研究低溫高真空環(huán)境下鋼材料的摩擦表現(xiàn)時發(fā)現(xiàn)鋼的表面出現(xiàn)變色現(xiàn)象。其低溫下的摩擦實驗是在外接低溫真空設(shè)備的球-盤式摩擦試驗機中進行的,當真空度低于 5×10-3 Pa 時開始降溫。
隨著溫度的變化,真空環(huán)境下剩余的微量氣體分子對鋼材料表面的物理性質(zhì)產(chǎn)生了影響,如圖3所示。圖中鋼表面呈現(xiàn)出藍紫色,且在升溫過程中(140~280 K)鋼表面顏色變化最為明顯。通過使用質(zhì)譜儀實時監(jiān)測真空室內(nèi)氣氛含量,證實了這種顏色變化是由真空設(shè)備中微量的水蒸氣造成的,同時影響著鋼材料表面摩擦學行為。研究發(fā)現(xiàn)摩擦過程中水分子的冷凝使鋼/鋼摩擦副的耐磨性提高,并且通過主動控制氣氛中氮氣和氧氣的含量可以進一步降低磨損。
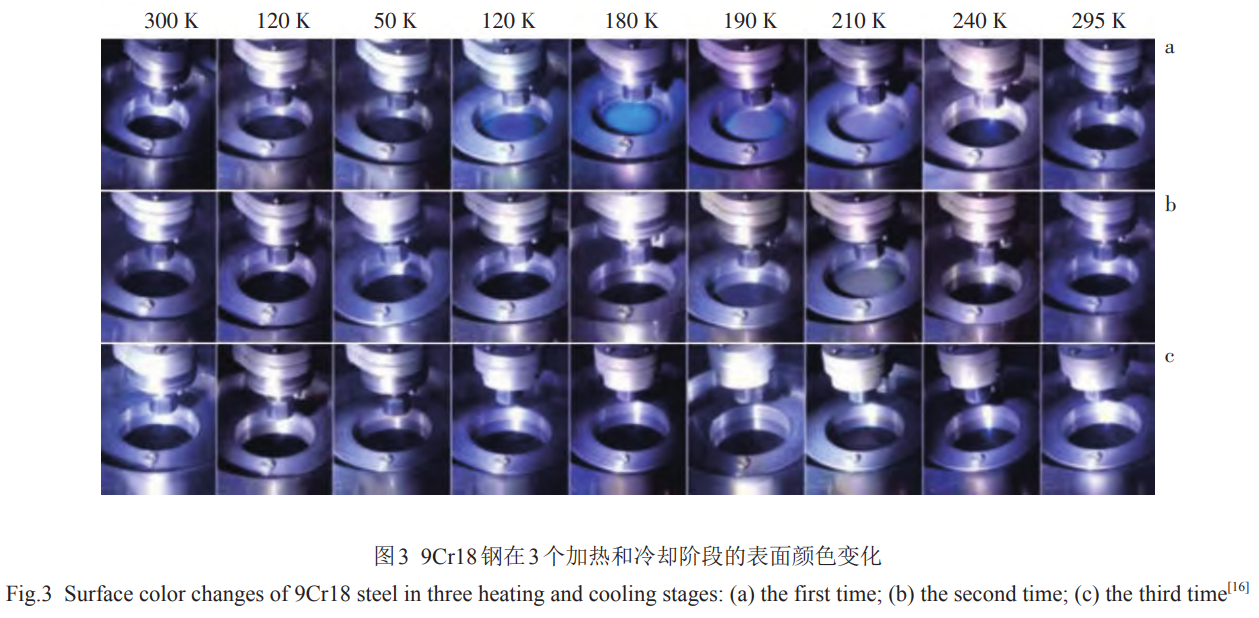
2.3 低溫真空介質(zhì)
由于低溫液體或氣體的存在,可能會引起介質(zhì)含量的變化或摩擦界面的轉(zhuǎn)變。因此,需要反復更換所需的測試氣體和含量監(jiān)測,以保證低溫下氣體環(huán)境的一致性。
此外,氣體介質(zhì)的物理性質(zhì)(如熱導率等)會影響材料在低溫下的摩擦學性能。而真空環(huán)境,尤其是超高真空環(huán)境,可以在很大程度上消除環(huán)境介質(zhì)對摩擦試驗結(jié)果的干擾。然而,在高度真空下缺乏溫度傳導介質(zhì),僅能通過導熱和輻射方式傳熱,制冷功率有限,因此在高速下進行的摩擦試驗結(jié)果可能是不準確的。2020年清華大學Cui等[17]在低溫真空下對聚合物基復合材料進行了測試,其自制的低溫摩擦設(shè)備如圖4所示。其設(shè)計最低溫度為–100 ℃,真空度為5×10-5 Pa。充滿液氮的水槽并不與摩擦副直接接觸,而是通過熱輻射傳熱。真空腔室溫度由加熱燈泡控制并由轉(zhuǎn)盤附近的熱電偶測量(圖中未畫出)。發(fā)現(xiàn)其在寬溫域內(nèi)保持摩擦系數(shù)小于0.1,并通過表征手段證明了轉(zhuǎn)移膜的生成,解釋了聚合物材料在低溫下摩擦系數(shù)與磨損率的特點。
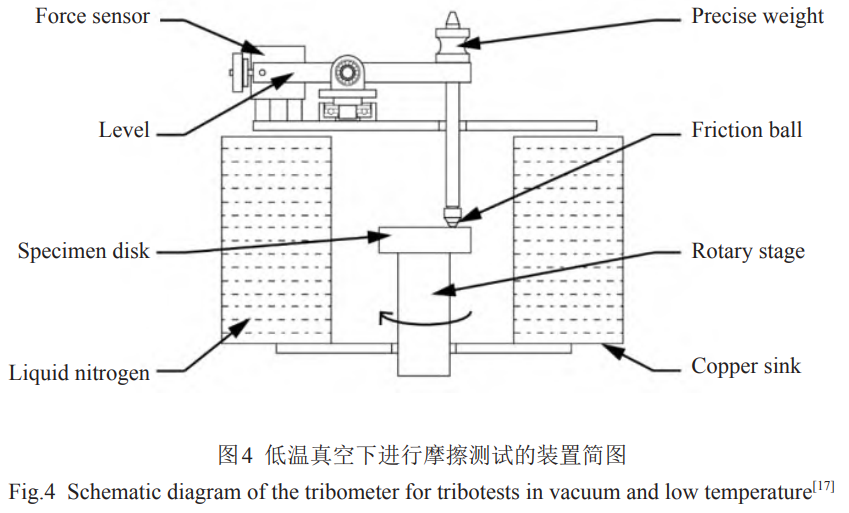
目前,低溫摩擦學的評價多集中于低溫液體介質(zhì),測試的溫度點不連續(xù)。而在實際工況當中,由于涉及真空、氣體環(huán)境和交變溫度等多種場景,這將造成測試結(jié)果與實際服役工況的差異。因此需要結(jié)合新型制冷技術(shù)設(shè)計探索新的低溫實驗測試方法與手段,進一步推動低溫摩擦學研究的發(fā)展。
3、金屬材料的低溫摩擦學性能
在低溫環(huán)境中,金屬材料的選擇至關(guān)重要,許多金屬材料在低溫下表現(xiàn)出良好的機械性能與摩擦學性能,因此被廣泛應(yīng)用于航空航天、低溫工程和極地航行等領(lǐng)域。
如在液化天然氣工業(yè)中不銹鋼被用于制造儲存罐和輸送管道,以確保安全和可靠的運輸;鋁合金在航空航天領(lǐng)域中被廣泛應(yīng)用于制造飛機機身和發(fā)動機零部件等;鈦合金可以用于制造航空發(fā)動機零部件、航天器結(jié)構(gòu)和海洋平臺設(shè)備,以承受極端溫度和壓力條件。
盡管在低溫環(huán)境下有多種金屬材料可供選擇,但鋼、鋁合金、鈦合金和高熵合金因其在低溫條件下表現(xiàn)出更優(yōu)異摩擦學特性逐漸成為學術(shù)界和工業(yè)界的研究重點,并展現(xiàn)出更廣闊的應(yīng)用前景,如可以支持在不同的低溫環(huán)境下工作的低碳錳鋼、中鎳鋼和鎳鉻奧氏體鋼。本部分將針對近期較為新穎的研究成果,對不同的金屬材料性能以及加工方法進行匯總綜述,以期使讀者可以快速了解近期金屬材料在低溫下的摩擦學研究進展。
3.1 鋼材料在低溫下的摩擦磨損性能
鋼是對含碳量質(zhì)量分數(shù)介于0.02%至2.11%之間的鐵碳合金的統(tǒng)稱。根據(jù)用途的不同,鋼的化學成分中含有不同的合金元素,比如添加了錳和鎳的鋼在低溫下有著更好的使用性能。如今,鋼以其低廉的價格、可靠的性能成為世界上使用最多的材料之一,是建筑業(yè)、制造業(yè)和人們?nèi)粘I钪胁豢苫蛉钡某煞帧?梢哉f鋼是現(xiàn)代社會的物質(zhì)基礎(chǔ)。為了進一步擴大低成本鋼材料的應(yīng)用,研究鋼材料在低溫下的性能勢在必行。低碳中錳鋼具有優(yōu)異的成形性、焊接性、強度和韌性,是汽車工業(yè)結(jié)構(gòu)件和先進工程厚鋼板的重要合金[18]
。
經(jīng)奧氏體逆轉(zhuǎn)處理(austenite reversion treatment, ART)[19]后,它們呈現(xiàn)出超細回火馬氏體和相當數(shù)量的亞穩(wěn)奧氏體的雙相組織,強度和塑性得到了額外的提高[20]。Yan
等[21]研究了ART處理后的中錳鋼(富奧氏體鋼)在20、0、–50和–120 ℃下的摩擦磨損行為。結(jié)果表明,馬氏體鋼和富奧氏體鋼的耐磨性隨磨損試驗溫度的降低而提高,馬氏體的硬度隨溫度降低而升高,但是其沖擊韌性急劇下降,富奧氏體鋼中亞穩(wěn)奧氏體產(chǎn)生的應(yīng)變硬化和韌性增強極大地降低了低溫下的磨損體積。與馬氏體鋼相比,主要的磨損機制從犁溝轉(zhuǎn)變?yōu)榍邢?。這一研究為開發(fā)低溫應(yīng)用的初始硬度相對較低的新型耐磨鋼提供了依據(jù)。
通過對鋼成分進行調(diào)控,可以在一定程度上改善其在低溫下的使用性能。為了提高低溫船舶用鋼的低溫摩擦磨損性能,上海海事大學的孫士斌等[22]設(shè)計并制備了4 種新型不同 Si 含量(0.3%、0.6%、0.9% 和 1.2%)的船用低溫高強鋼,研究并分析了其摩擦磨損性能。結(jié)果顯示:
在恒定低載荷(20 N)和恒定低滑動速率(10 mm/s)條件下,該新型船用鋼板的磨痕表面硬度明顯高于磨損前,摩擦機理以粘著磨損、疲勞磨損為主,部分區(qū)域發(fā)生氧化磨損,磨屑被擠壓產(chǎn)生加工硬化層。這是由于Si的添加起到了固溶強化以及相變強化的綜合作用,顯著提高了鋼材料的摩擦磨損性能以及硬度。其中,Si含量為1.2%的船用低溫鋼在20和–10 ℃下均表現(xiàn)出優(yōu)異的摩擦磨損性能,平均摩擦系數(shù)分別為0.41(20 ℃)、0.38(–10 ℃);磨損 量 分 別 為 1.695×10-5 m3(20 ℃ )、2.097×10-5 m3(–10 ℃)。隨著Si含量的上升,使得經(jīng)過兩相區(qū)調(diào)質(zhì)熱處理的船用低溫鋼金相組織不同程度細化,并且使得固溶強化不斷加強,磨損量降低,鋼材在低溫條件下的耐磨性有所提高。
3.2 鈦合金在低溫下的摩擦磨損性能
鈦合金具有密度低、比強度高、耐腐蝕性能好和低溫力學性能優(yōu)異等特點,是航空航天領(lǐng)域應(yīng)用最廣泛的材料之一,在火箭發(fā)動機的貯箱、低溫液體貯箱、緊固件、泵葉輪、支架等低溫部件應(yīng)用廣泛[23–25]。然而,塑性剪切抗力較低以及表面氧化物的保護作用較弱[26]導致鈦及其合金的摩擦學性能較差,嚴重限制了鈦合金的進一步應(yīng)用。
例如,在鈦合金構(gòu)件的實際應(yīng)用過程中,摩擦副表面的氧化膜會發(fā)生磨損損失[27]從而失去保護作用。為了提高鈦合金的耐磨性 ,人們對其進行大量改性處理 ,如滲氮[28–29],涂層處理[30],摻雜[31–32]等。得益于多種改性手段,截至目前已經(jīng)涌現(xiàn)出了一批在低溫領(lǐng)域摩擦性能表現(xiàn)優(yōu)良的鈦合金材料。
中國石油大學的Wang等[33]測試了Invar36低膨脹鎳鈦合金在低溫下的性能。實驗結(jié)果表明Invar36合金具有優(yōu)異的摩擦學性能,其摩擦系數(shù)(coefficient of friction, COF)在 20~–78 ℃范圍內(nèi)逐漸減小。隨著溫度降至 –196 ℃,COF也隨著溫度下降而急劇下降,至–196 ℃時達到最小值。此外,在相同條件下對一種商業(yè)軸承級材料(G95Cr18鋼)進行了測試和比較,結(jié)果表明Invar36合金具有比G95Cr18鋼更好的摩擦學性能,在–196 ℃時,其磨損率比 G95Cr18 鋼低 55.43%。進一步的模擬對比表明,由于其極低的熱膨脹系數(shù),在低溫條件下,Invar36合金比G95Cr18鋼具有更高的韌性和強度。該研究提供了Invar36鈦合金在不同溫度和載荷下對Si3N4陶瓷球的摩擦學數(shù)據(jù),為開發(fā)出低溫具有高耐磨的鈦合金發(fā)展提供了重要的理論指導。
Ti基塊體金屬玻璃復合材料通常具有優(yōu)異的強度、塑性和韌性,因而成為低溫工程應(yīng)用的潛在理想選擇之一[34]。然而,關(guān)于其磨損行為的研究仍然較為稀缺。Ren等[35]研究了Ti基塊體金屬玻璃復合材料在113 K的低溫下的耐磨性,在低溫下Ti基金屬玻璃復合材料的耐磨性大大提高。Ti47.2Zr33.9Cu5.9Be13金屬玻璃復合材料的低溫摩擦性能如圖5所示。
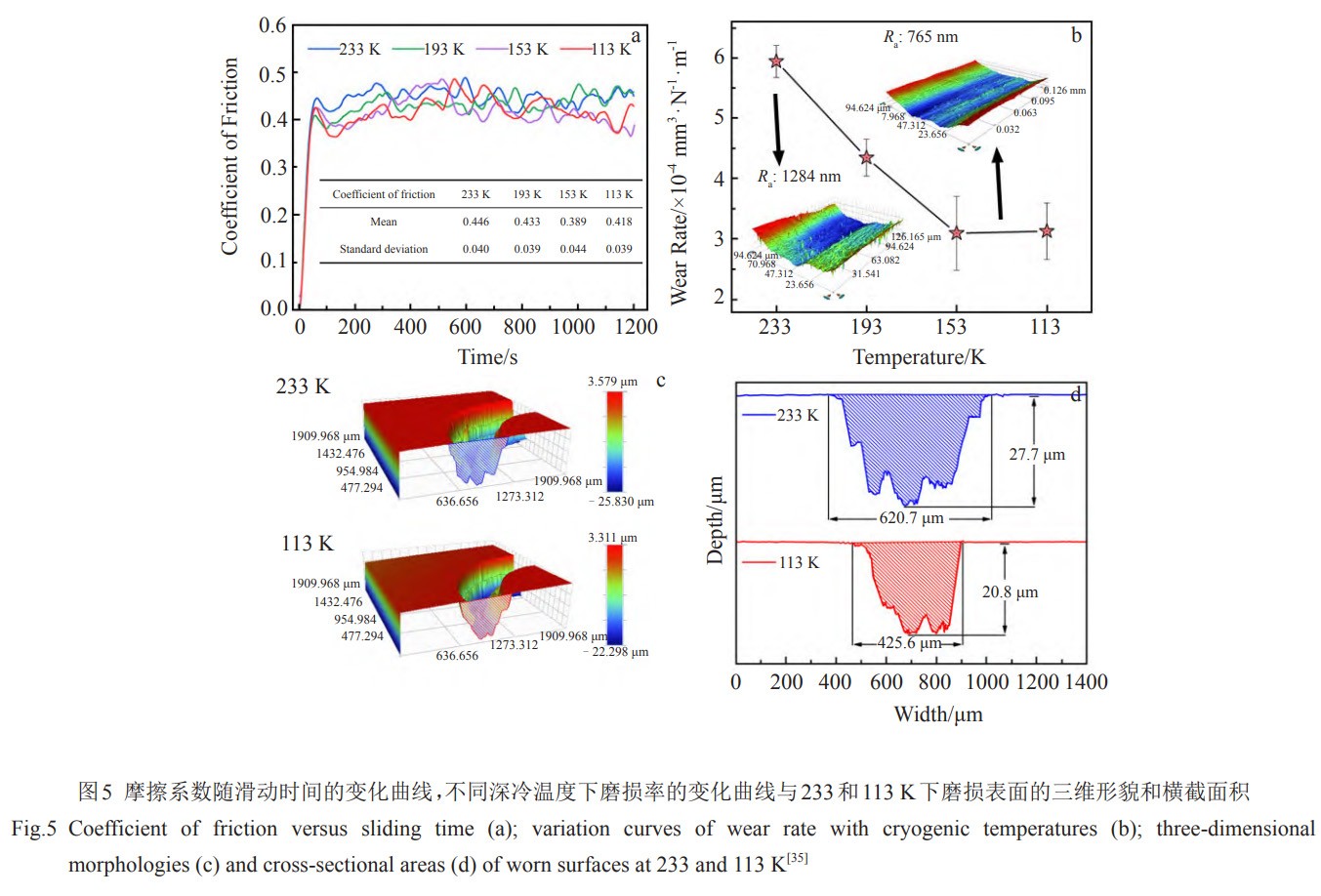
圖5a展示了其在不同溫度下的摩擦系數(shù),隨著溫度的降低,動摩擦因數(shù)略有降低;在圖 5b 中 ,當溫度從 233 K 降低到 113 K 時 ,磨損率從5.95×10-4 mm3/(N·m)單調(diào)降低到3.12×10-4 mm3/(N·m),磨損率降低高達47.6%。由磨痕的三維形貌(圖5b)可知在低溫下測試的磨損表面呈現(xiàn)更光滑和輕微的表面,粗糙度更低。圖5c展示了從3D輪廓儀獲得的磨損軌跡的整體 3D 視圖。與 233 K 相比,Ti47.2Zr33.9Cu5.9Be13金屬玻璃復合材料在113 K下摩擦時具有更窄、更淺的磨痕。研究結(jié)果證明該 Ti 基塊體金屬玻璃復合材料在較低的低溫下具有更好的耐磨性。
3.3 鋁合金在低溫下的摩擦磨損性能
與金屬鈦相比,鋁合金有著更低的密度,并且添加一定合金化元素后可達到較高強度,其比強度接近高合金鋼而比剛度超過鋼,具有良好的鑄造性能和塑性加工性能[36]。因此在航空航天、交通運輸、建筑、機電等方面有著廣泛的應(yīng)用。此外,低溫環(huán)境下可以同時改善鋁合金的硬化和塑性能力[37–38],可以克服其室溫成形性差的問題,因此也被視為具有優(yōu)異低溫摩擦的理想材料之一。
中國科學院北京物理與化學研究所低溫技術(shù)重點實驗室的Weng等[39]研究了15% SiC顆粒/2009Al鋁基復合材料在室溫和低溫滑動磨損條件下的亞表面變形和磨損行為。結(jié)果表明,與室溫相比,低溫下的滑動實驗在亞表層引起了更大的塑性變形。這是因為在低溫下鋁基體塑性增加以及SiC顆粒脆性增加導致其對鋁合金基體變形的阻礙作用降低。在低溫下進行滑動實驗的復合材料的磨損率顯著降低。磨損表面在低溫滑動后具有較低的表面粗糙度和較高的表面均勻性。磨損機制由室溫下嚴重的氧化磨損、粘著磨損和剝層磨損轉(zhuǎn)變?yōu)榈蜏鼗瑒酉螺p微的剝層磨損和開裂特征。低溫滑動后的變形層起到了納米晶加工硬化層的作用,低溫下加工硬化率和位錯密度增加,抑制了裂紋的產(chǎn)生,相應(yīng)地提高了材料的磨損性能。這項研究為通過在低溫環(huán)境下自適應(yīng)形成納米硬化層的方法來設(shè)計高表面性能的鋁基復合材料提供了一種新的策略。
鋁合金超低溫成形過程中溫度分布不同,模具與鑄件的界面之間接觸壓力隨材料流動不斷變化,接觸面之間的摩擦形式也會隨之改變。Gao等[40]研究了高壓低溫下鋁合金的減摩機理。結(jié)果表明,COF隨著壓力的增加先增大后減小。溫度的降低以及接觸面壓力的增加,均有利于鋁合金組織的晶粒尺寸的減小,導致粘著摩擦或犁溝摩擦減少,從而導致在高壓和低溫下的COF較低;較高的溫度和壓力則增加了粘著力,容易引起黏著磨損的發(fā)生,不利于延長模具的使用壽命??梢娋氉冃挝⒔Y(jié)構(gòu)的形成增強了表面材料的塑性和抵抗變形的能力,該工作不僅有助于推進多尺度摩擦模型的建立,而且為低溫成形仿真和工藝參數(shù)優(yōu)化提供了基礎(chǔ)。
3.4 多主元合金在低溫下的摩擦磨損性能
傳統(tǒng)合金通常是以1種或2種金屬元素作為基元,向其中添加金屬或者非金屬元素以達到強化金屬使用性能的目的。隨著工業(yè)領(lǐng)域的快速發(fā)展,傳統(tǒng)合金的研發(fā)陷入瓶頸。近年來,由我國臺灣科學家Yeh教授[41]和英國學者 Cantor 教授[42]提出了 1 種新型多主元合金設(shè)計理念,其顛覆了傳統(tǒng)合金由單一主元構(gòu)成的設(shè)計理念,為合金材料的成分組成、組織調(diào)控與性能設(shè)計帶來了廣闊的開發(fā)空間。與傳統(tǒng)合金相比,多主元合金由于兼具高強度、高硬度、抗磨損性能與耐腐蝕性能受到了人們的廣泛關(guān)注。多主元合金[43]的設(shè)計理念使得合金成分呈現(xiàn)爆發(fā)式增長,極大拓寬了金屬材料的成分空間,將人們的關(guān)注點從相圖的角落位置轉(zhuǎn)到廣闊的中間區(qū)域[44],而復雜的成分賦予了合金組織與性能上諸多的可能性,開啟了新型多主元合金的研究熱潮。
CoCrNi多主元合金由于在低溫下沒有明顯的韌脆轉(zhuǎn)變并且在很寬的溫度范圍內(nèi)都有很好的強塑性[45],已被公認為低溫應(yīng)用的 fcc 多主元合金的典型代表體系[46–48]。Ren等[49]研究了CoCrNi多主元合金在低溫下的摩擦學行為,研究表明 CoCrNi 多主元合金在溫度從 273 K降低到153 K時表現(xiàn)出顯著增強的耐磨性,超過了低溫奧氏體鋼。通過顯微觀察和原子模擬,明確了影響CoCrNi低溫耐磨性能的變溫組織特征和變形機制。在深冷條件下,顯著的晶粒細化和較深的塑性區(qū)導致了向表面以下擴展的組織梯度,這可以容納大量的滑動變形,這與273 K下的應(yīng)變局部化和分層形成了直接的對比。
同時,與溫度相關(guān)的深冷變形機制(堆垛層錯網(wǎng)絡(luò)與相變)也為亞表層材料提供了額外的強化和增韌。這些特性使得 CoCrNi 合金在低溫條件下特別耐磨損。圖 6 所示為奧氏體合金鋼與CoCrNi基高熵合金在不同溫度下磨損率對比,可以看出奧氏體合金鋼在低溫下的摩擦磨損性能并不突出,對于某些成分的合金鋼,低溫甚至會增大其磨損率(06Cr19Ni10鋼)。而CoCrNi多主元合金不僅在常溫下有著較低的磨損,在低溫下其耐磨性能大大提高,與室溫相比降低了44%,是在低溫下性能優(yōu)異的金屬材料。
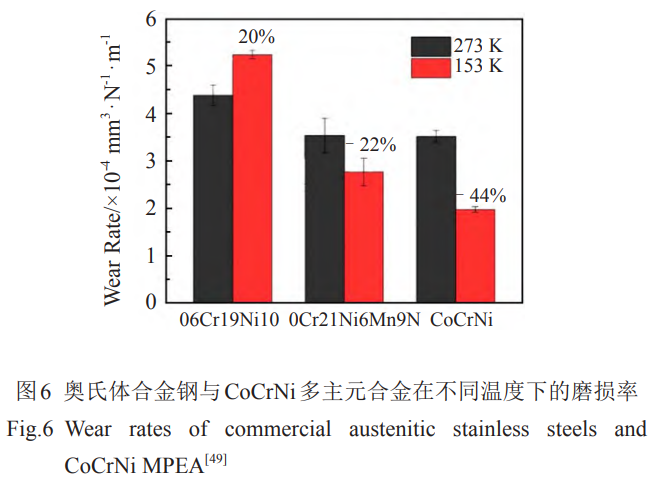
MPEA 具有極高的構(gòu)型熵,由 5 種及以上主元組成的 MPEA 被 稱 為 高 熵 合 金(high-entropy alloys, HEAs)[50-52]。Geng等[53]研究了單相CoCrFeNiMn高熵合金和CoCrFeNiAl高熵合金在低溫真空環(huán)境下的摩擦學行為,結(jié)果表明 173 K 下單相 CoCrFeNiMn 高熵合金和 CoCrFeNiAl 高 熵 合 金 均 有 高 的 耐 磨 性 ,其 中CoCrFeNiAl 高熵合金磨損率可低至 1×10-6 mm3/(N·m)。并且在摩擦過程中的接觸應(yīng)力以及瞬時溫度的提高促進了HEAs的晶粒細化,這更進一步使得HEAs的耐磨性提高。這項工作進一步通過多種表征手段研究了在2種接觸條件下的磨損誘導微觀組織演變,填補了低溫下高性能高熵合金摩擦學行為的空白,為進一步優(yōu)化高熵合金在低溫下的耐磨性提供了指導。
4、總結(jié)與展望
本文介紹了金屬材料低溫摩擦研究現(xiàn)狀,包括低溫摩擦學的實驗技術(shù)以及目前新穎的金屬材料研究進展。
首先概述了金屬材料在低溫下服役所遇到的困境,包括低溫潤滑失效以及低溫脆韌轉(zhuǎn)變。對于材料在低溫下的摩擦學試驗環(huán)境進行了總結(jié)和討論,分別介紹了低溫液體介質(zhì)、低溫氣體介質(zhì)和低溫真空介質(zhì)環(huán)境的優(yōu)缺 點。根據(jù)金屬材料的種類不同,分別介紹了低溫下的鋼材料、鈦合金材料、鋁合金材料以及多主元合金材料的前沿成果,其中多主元合金作為新興領(lǐng)域,在低溫下表現(xiàn)出了優(yōu)異的耐磨性,是未來最具潛力的新型材料之一。
隨著航空事業(yè)、低溫超導、氫能源動力相關(guān)技術(shù)的不斷發(fā)展,低溫的應(yīng)用會越來越廣泛,由此引發(fā)的潤滑問題仍需要進一步研究。就目前而言低溫潤滑仍有若干問題需要解決與完善。首先,由于大部分低溫摩擦實驗是在低溫液體介質(zhì)中進行的,導致測試的溫度點比較單一。
然而實際使用過程中的外界環(huán)境復雜多變,測試環(huán)境與實際使用環(huán)境存在差異。因此需要開發(fā)更加契合使用環(huán)境的實驗方法;其次,現(xiàn)有的低溫實驗表征手段大多在室溫下進行,難以獲得低溫下材料的實時變化信息;最后,低溫摩擦學的諸多研究仍不夠系統(tǒng),其機理部分的研究還不夠深入。
綜上所述,金屬材料低溫摩擦研究領(lǐng)域雖然取得了顯著進展,但仍存在諸多挑戰(zhàn)和未知。未來的研究應(yīng)著力于開發(fā)更為適用的實驗方法和表征手段深入探討 低溫摩擦機理,進一步研究不同材料在不同因素影響下的摩擦行為,以推動具有優(yōu)異耐磨性金屬材料的發(fā)展和應(yīng)用。
參考文獻 References
[1] Sápi Zsombor, Butler Richard. Cryogenics[J], 2020, 111: 103190
[2] Li Yu, Li Wei, Wang Bingjun et al. Science Bulletin[J], 2023, 68(12): 1243
[3] Wen Shizhu(溫詩鑄), Huang Ping(黃 平). Principles of Tribology(摩擦學原理)[M]. Beijing: Tsinghua University Press, 2012
[4] Wang Dongsheng(王東勝), Chang Xueting(常雪婷), Wang Shiyue(王士月) et al. Journal of Chongqing University(重慶大學學報)[J], 2018, 41(6): 66
[5] Zhu Yongqi(朱永琪), Li Hongxuan(李紅軒), Ji Li(吉 利) et al. Tribology(摩擦學報)[J], 2023, 43(9): 1083
[6] Shi Yeran, Wang Wan, Zhou Qing et al. ACS Applied Materials & Interfaces[J], 2024, 16(22): 29453
[7] Menezes P L, Rohatgi P K, Omrani E. Self-Lubricating Composites[M]. Berlin: Springer, 2022
[8] Gradt Thomas, Schneider Thomas. Lubricants[J], 2016, 4(3): 32
[9] Hübner W, Gradt T, Schneider T et al. Wear[J], 1998, 216(2): 150
[10] Edward Jay Epstein. The Rise and Fall of Diamonds: the Shattering of a Brilliant Illusion[M]. New York: Simon and Schuster, 1982
[11] Cui Wenyan, Chen Hongzhan, Zhao Jianxun et al. International Journal of Extreme Manufacturing[J], 2023, 5(2): 022004
[12] Theiler Géraldine, Gradt Thomas. Cryogenics[J], 2018, 93: 1
[13] Wisander D W, Maley C E, Johnson R L. ASLE Transactions[J], 1959, 2(1): 58
[14] Iwabuchi A, Honda T, Tani J. Cryogenics[J], 1989, 29(2): 124
[15] Yu Chengguo(尉成果), Chen Wanhua(陳萬華), Liang Bo(梁 波) et al. Scientia Sinica Technologica( 中 國 科 學) [J], 2020, 50(6): 775
[16] Zhu Yongqi, Li Hongxuan, Li Fengying et al. Tribology International[J], 2024, 191: 109104
[17] Cui Wenyan, Raza Khalid, Zhao Zhijun et al. Tribology International[J], 2020, 152: 106569
[18] Lee Y K, Han J. Materials Science and Technology[J], 2015, 31(7): 843
[19] Wang C, Cao W, Shi J et al. Materials Science and Engineering A[J], 2013, 562: 89
[20] Srivastava A K, Jha G, Gope N et al. Materials Characterization[J], 2006, 57(2): 127
[21] Yan X C, Hu J, Wang L Y et al. Wear[J], 2021, 486–487: 204116
[22] Sun Shibin(孫士斌), Yang Ti(楊 剔), Wang Dongsheng(王東勝) et al. Materials Protection(材料保護)[J], 2020, 53(4): 15
[23] Banerjee D, Williams J C. Acta Materialia[J], 2013, 61(3): 844
[24] El-Tayeb N S M, Yap T C, Venkatesh V C et al. Materials & Design[J], 2009, 30(10): 4023
[25] Xu Wei, Lu Xin, Tian Jingjing et al. Journal of Materials Science & Technology[J], 2020, 41: 191
[26] Molinari A, Straffelini G, Tesi B et al. Wear[J], 1997, 208(1–2): 105
[27] Liu Yong(劉 勇), Ye Zhuyu(葉鑄玉), Yang Dezhuang(楊德莊) et al. Journal of Harbin Institute of Technology(哈爾濱工業(yè)大學學報)[J], 2006, 38: 335
[28] Courant B, Hantzpergue J J, Benayoun S. Wear[J], 1999, 236(1–2): 39
[29] Belkin P N, Kusmanov S A, Zhirov A V et al. Journal of Materials Science & Technology[J], 2016, 32(10): 1027
[30] Heinrich G, Gr?gler T, Rosiwal S M et al. Surface and Coatings Technology[J], 1997, 94–95: 514
[31] Schmidt H, Schminke A, Rück D M. Wear[J], 1997, 209(1–2): 49
[32] Allen C, Bloyce A, Bell T. Tribology International[J], 1996, 29(6): 527
[33] Wang Bin, Guo Yanbao, Zhang Zheng et al. Wear[J], 2023, 518–519: 204648
[34] Zhou Qing, Ren Yue, Du Yin et al. Journal of Alloys and Compounds[J], 2019, 780: 671
[35] Ren Yue, Yan Tingyi, Huang Zhuobin et al. Journal of Materials Science & Technology[J], 2023, 134: 33
[36] Deng Lei, Wang Xinyun, Jin Junsong et al. Frontiers of Mechanical Engineering[J], 2018, 13(1): 25
[37] Kumar M, Sotirov N, Grabner F et al. Transactions of Nonferrous Metals Society of China[J], 2017, 27(6): 1257
[38] Huang Ke, Huang Shiquan, Yi Youping et al. Journal of Alloys and Compounds[J], 2022, 902: 163821
[39] Weng Zeju, Pan Ran, Liu Baosheng et al. Ceramics International[J], 2023, 49(11): 17135
[40] Gao Yiren, Li Hongxia, Zhao Danyang et al. Journal of Materials Research and Technology[J], 2024, 28: 1538
[41] Yeh J W, Chen S K, Lin S J et al. Advanced Engineering Materials[J], 2004, 6(5): 299
[42] Cantor B, Chang I T H, Knight P et al. Materials Science and Engineering A[J], 2004, 375–377: 213
[43] Ye Y F, Wang Q, Lu J et al. Materials Today[J], 2016, 19(6): 349
[44] Yeh J W, Chen Y L, Lin S J et al. Materials Science Forum[J], 2007, 560: 1
[45] Lu Kaiju, Chauhan Ankur, Tirunilai Aditya Srinivasan et al. Acta Materialia[J], 2021, 215: 117089
[46] Gludovatz B, Hohenwarter A, Thurston K V S et al. Nature Communications[J], 2016, 7: 10602
[47] Liu Dong, Yu Qin, Kabra Saurabh et al. Science[J], 2022, 378(6623): 978
[48] Rackwitz Julian, Yu Qin, Yang Yang et al. Acta Materialia[J], 2020, 200: 351
[49] Ren Yue, Zhou Qing, Hua Dongpeng et al. Science Bulletin[J], 2024, 69(2): 227
[50] Gao Qiuyu, Wei Ran, Feng Shilin et al. Scripta Materialia[J], 2023, 228: 115334
[51] Wu Z, Bei H, Pharr G M et al. Acta Materialia[J], 2014, 81: 428
[52] Gludovatz Bernd, Hohenwarter Anton, Catoor Dhiraj et al. Science[J], 2014, 345(6201): 1153
[53] Geng Yushan, Liu Jian, Cheng Jun et al. Materials Science and Engineering A[J], 2024, 894: 146185
相關(guān)鏈接