1、引言
目前國(guó)內(nèi)外新興的金屬增材制造技術(shù)打印技術(shù)為新產(chǎn)品的制造帶來了革命性的突破,在很大程度上改變了傳統(tǒng)的思維方式和固有的研發(fā)流程,實(shí)現(xiàn)了復(fù)雜產(chǎn)品構(gòu)件設(shè)計(jì)制造的高質(zhì)量快速響應(yīng)。歐美等世界各國(guó)的高度重視金屬增材制造技術(shù)快速發(fā)展。尤其對(duì)該技術(shù)在航空航天領(lǐng)域的應(yīng)用開展了大量研究工作并將這一先進(jìn)技術(shù)工程化。美國(guó)航空航天局已于2012年底開始打印零件并用于下一代大推力火箭的測(cè)試。2013年8月,NASA對(duì)用3D打印技術(shù)制作出的火箭發(fā)動(dòng)機(jī)噴射器進(jìn)行了成功測(cè)試。歐洲宇航防務(wù)集團(tuán)創(chuàng)新工場(chǎng)和歐洲光學(xué)學(xué)會(huì)使用直接金屬激光燒結(jié)技術(shù)制造的鈦零件替代空客A320發(fā)動(dòng)機(jī)艙的鑄鋼鉸鏈支架。在關(guān)鍵載荷位置優(yōu)化金屬結(jié)構(gòu)布置,削減了75%的原材料重量。
金屬3D打印也叫金屬增材制造?;诮o粉的方式不同,3D打印技術(shù)主要分為兩大類:基于同步送粉激光熔覆技術(shù)發(fā)展起來的成型技術(shù),本項(xiàng)目采用的3D打印技術(shù)是目前成形最精密的SLM(精密選區(qū)熔化)技術(shù),基于快速成形的最基本思想即逐層熔覆的增材制造方式,根據(jù)零件的三維模型。將模型按一定的厚度切片分層,即將零件的三維形狀信息轉(zhuǎn)換成一系列二維輪廓信息,隨后在數(shù)控系統(tǒng)的控制下,用激光通過陣鏡控制來熔化金屬粉末,直接成形具有特定幾何形狀的零件。成形過程中金屬粉末完全熔化,熔化的粉末制件產(chǎn)生良好的冶金結(jié)合。由于SLM技術(shù)可直接獲得幾乎任意形狀、具有完全冶金結(jié)合、高精度的近乎致密金屬零件,應(yīng)用范圍比較廣,主要是航空航天領(lǐng)域的超輕結(jié)構(gòu)件、機(jī)械領(lǐng)域的工具及模具、生物醫(yī)療領(lǐng)域等。它主要特點(diǎn)是:不去除材料的毛坯表面精度可到達(dá)Ra6.3μm,與部分機(jī)加工方式精度相當(dāng);成形精度高,可獲得0.1mm的立方網(wǎng)格結(jié)構(gòu)體;由于SLM光斑集中,成形過程熔池大小≤0.1mm,沉積成形體材料內(nèi)部組織非常細(xì)小、均勻,晶粒尺寸達(dá)到微米級(jí);致密度幾乎能達(dá)到100%。零件機(jī)械性能與鍛造工藝所得相當(dāng),綜合性能優(yōu)異。本項(xiàng)目需采用TC11高溫鈦合金材料實(shí)現(xiàn)航天高精度復(fù)雜零件SLM增材制造并應(yīng)用目前在國(guó)內(nèi)還較少,需進(jìn)行相關(guān)設(shè)計(jì)制造技術(shù)研究。
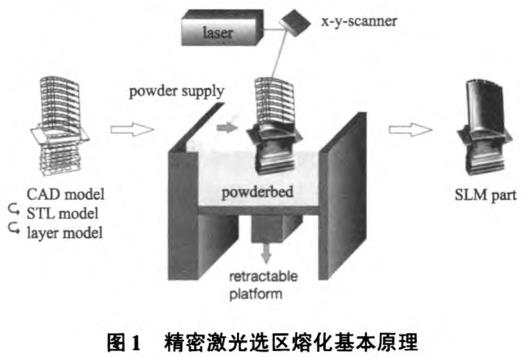
提高產(chǎn)品結(jié)構(gòu)的功率質(zhì)量比對(duì)航天產(chǎn)品意義十分重大。航天高溫鈦合金結(jié)構(gòu)件復(fù)雜的產(chǎn)品制造過程可通過開展基于SLM技術(shù)的設(shè)計(jì)、制造研究而高效、集約實(shí)現(xiàn)。即首先通過有限元分析計(jì)算及專業(yè)軟件實(shí)現(xiàn)基于SLM增材制造結(jié)構(gòu)的輕量化、一體化設(shè)計(jì):其次通過合理優(yōu)化的工藝參數(shù)和后續(xù)熱處理來實(shí)現(xiàn)SLM增材制造零件制備;之后應(yīng)用技術(shù)研究包括SLM增材制造高溫鈦合金難加工材料的切削性能研究、SLM增材制造零件的精密機(jī)械加工技術(shù)研究、基于SLM技術(shù)產(chǎn)品檢測(cè)與試驗(yàn)方法研究等實(shí)現(xiàn)實(shí)際應(yīng)用。通過以上研究解決了零件快速成型問題,減輕零件重量,改善切削加工性能,提高產(chǎn)品質(zhì)量,縮短生產(chǎn)周期,滿足使用要求。
2、產(chǎn)品特點(diǎn)
本課題產(chǎn)品工作環(huán)境惡劣,工作工質(zhì)為約1200℃的高溫氣體,表面工作溫度達(dá)(400~500)℃,承載著高達(dá)幾萬轉(zhuǎn)的工作轉(zhuǎn)速的輪系。為了滿足惡劣環(huán)境和減重設(shè)計(jì)要求,對(duì)材料高溫性能要求高,且結(jié)構(gòu)與制造過程復(fù)雜。原產(chǎn)品由前殼體A、前殼體B、進(jìn)氣嘴、后殼體、排氣管、左、右支架、壓板共12個(gè)零件組成,通過鍛造、焊接、熱處理、精密機(jī)加、組合機(jī)加、裝配等工藝環(huán)節(jié)組裝成殼體組合件,主要制造過程見圖2。
產(chǎn)品制造過程中主要存在以下問題:①制造周期長(zhǎng)。產(chǎn)品從備料到產(chǎn)出需六個(gè)月時(shí)間;②材料利用率低。整體材料利用率為21.3%,材料浪費(fèi)嚴(yán)重:③焊接難度大。耐高溫鈦合金材料焊接需要保護(hù),大厚度封閉焊縫需多層焊接并容易產(chǎn)生裂紋;④加工難度大。渦輪殼體尺寸加工要求高,但由于多次焊接、熱處理造成殼體變形大,另外殼體結(jié)構(gòu)復(fù)雜,需要較多的工裝保證加工尺寸:⑤裝配難度大。渦輪殼體與支架安裝處由于焊接變形和無法二次機(jī)加,裝配時(shí)與渦輪支架裝配間隙大,降低了結(jié)構(gòu)剛度,易造成裝配過約束。
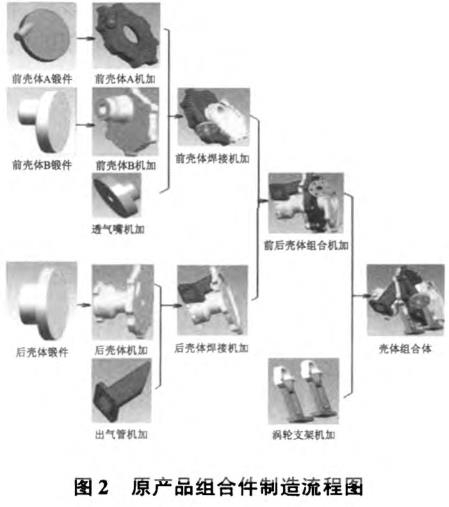
3、基于SLM增材制造的功能最優(yōu)一體化、輕量化設(shè)計(jì)
實(shí)現(xiàn)過程首先在于設(shè)計(jì)基于SLM技術(shù)優(yōu)先關(guān)注功能的實(shí)現(xiàn),不考慮制造工藝。通過有限元分析計(jì)算及專業(yè)的金屬3D打印模型設(shè)計(jì)、處理軟件實(shí)現(xiàn)基于SLM技術(shù)的功能最優(yōu)一體化、輕量化的設(shè)計(jì)技術(shù)。
采用一體化設(shè)計(jì):在滿足現(xiàn)有產(chǎn)品性能和接口要求的前提下,首先對(duì)渦輪殼體進(jìn)行了結(jié)構(gòu)一體化設(shè)計(jì),由原來12個(gè)零件縮減至兩個(gè)零件。通過仿真計(jì)算,為殼體的3D打印提供依據(jù)。模型如圖3所示。
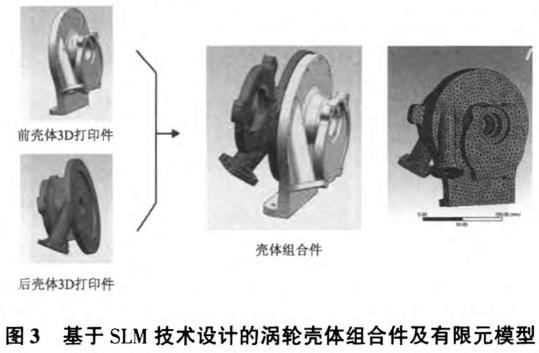
輕量化設(shè)計(jì):通過專業(yè)軟件對(duì)殼體非主承力部位進(jìn)行鏤空結(jié)構(gòu)處理,應(yīng)用拓?fù)渚W(wǎng)狀結(jié)構(gòu),保證結(jié)構(gòu)體剛度強(qiáng)度的情況下,保證壁厚不變及避開安裝孑L的情況下,獲得更大的減重效率模型薄壁邊界與內(nèi)部構(gòu)建中空網(wǎng)格支撐形狀如圖4。
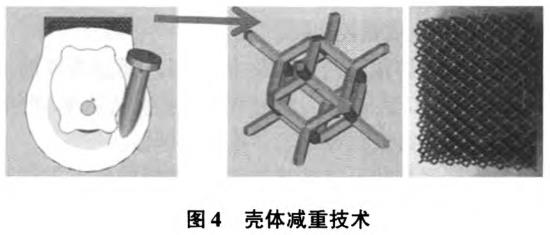
殼體結(jié)構(gòu)功能優(yōu)化設(shè)計(jì):利用專業(yè)的金屬3D打印模型設(shè)計(jì)處理軟件對(duì)殼體結(jié)構(gòu)進(jìn)行功能化結(jié)構(gòu)設(shè)計(jì)、優(yōu)化處理,使殼體構(gòu)件更加趨于完全功能化。如采取新的結(jié)構(gòu)設(shè)計(jì)對(duì)殼體構(gòu)件筋條進(jìn)行處理。
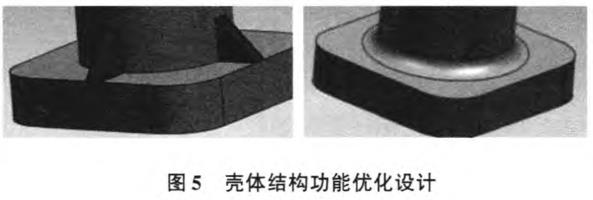
4、SLM成形工藝技術(shù)
項(xiàng)目采用TC11高溫鈦合金實(shí)現(xiàn)殼體制造。TC11高溫鈦合金工作溫度可達(dá)500℃以上,但成型過程變形與開裂的傾向大。對(duì)產(chǎn)品在激光選區(qū)熔化成形過程中會(huì)發(fā)生變形的部位,通過整體支撐加固、薄壁加厚、不同輔助支撐結(jié)構(gòu)措施來自由成形產(chǎn)品中的復(fù)雜結(jié)構(gòu):經(jīng)過金屬3D打印專用軟件的系統(tǒng)運(yùn)算、模擬對(duì)比,最終確定局部支撐形貌。優(yōu)化支撐結(jié)構(gòu)也解決了鈦合金激光選區(qū)熔化過程中的變形開裂問題:
SLM增材制造構(gòu)件內(nèi)部質(zhì)量和性能的控制主要是通過合理優(yōu)化的工藝參數(shù)和后續(xù)熱處理來實(shí)現(xiàn)。
1)設(shè)備:采用EOS M280型選擇性激光熔化設(shè)備。400W光纖激光器,最大零件成形尺寸為250mm×250mm×300mm,成形過程中通過惰性氣體對(duì)成形零件進(jìn)行保護(hù)。

2)基材:鈦合金板
3)激光選區(qū)熔化代碼生成:在激光選區(qū)熔化之前確定成形件的三維模型。然后通過Magics軟件對(duì)模型進(jìn)行處理,最終生成支撐。然后將處理好的模型Rp—Tools切片分層生成程序文件,最終生成數(shù)控代碼。
4)激光選區(qū)熔化工藝參數(shù)及生產(chǎn)過程:通過合理的工藝試驗(yàn)驗(yàn)證,嚴(yán)格控制成形工藝過程,確保激光功率、掃描速度、掃描路徑、氣氛控制等工藝參數(shù)的合理性。
5)激光選區(qū)熔化殼體的熱處理:根據(jù)新的成形方法對(duì)傳統(tǒng)標(biāo)準(zhǔn)熱處理工藝進(jìn)行調(diào)整,建立與SLM增材制造工藝及TC11高溫鈦合金相匹配的熱處理制度(雙退火),改善材料內(nèi)部組織和殘余應(yīng)力狀態(tài)。調(diào)整零件性能。
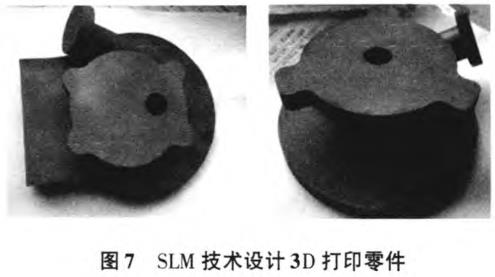
5、SLM增材制造高溫鈦合金零件切削性能研究
5.1 SLM增材制造高溫鈦合金材料切削性能研究
SLM增材制造的TC11耐高溫鈦合金材料為新型難加工材料。具有高溫強(qiáng)度、硬度高,熱導(dǎo)率低,精密切削加工過程中切削溫度高,加工變形大,刀具易磨損的難加工特點(diǎn)。選擇各種切削刀具。針對(duì)SLM增材制造耐高溫鈦合金材料車削、銑削、磨削精密切削加工過程開展切削性能研究。研究SLM增材制造高溫鈦合金材料切削過程中的與切削參數(shù)以及刀具和切削參數(shù)之間的關(guān)系,掌握材料切削性能。將切削性能研究成果進(jìn)行實(shí)際應(yīng)用,促進(jìn)高效率、高精度、高性能SLM增材制造技術(shù)的應(yīng)用,參數(shù)選擇見圖8。
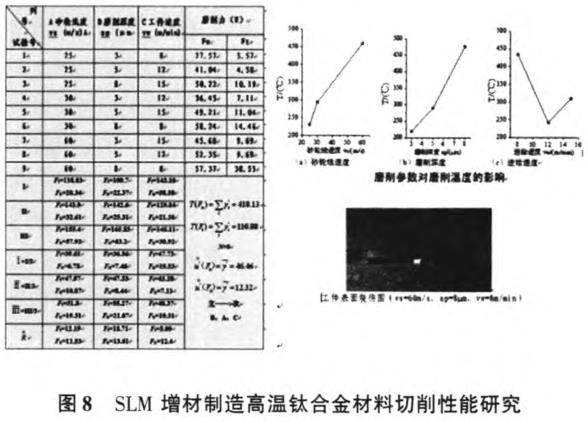
5.2 SLM增材制造零件的精密機(jī)械加工技術(shù)研究
1)工藝流程設(shè)計(jì):整體設(shè)計(jì)的零件復(fù)雜,空間交匯點(diǎn)多,需滿足眾多關(guān)鍵技術(shù)要求。精度要求達(dá)微米級(jí)。結(jié)合SLM復(fù)雜殼體的特點(diǎn)進(jìn)行工藝流程設(shè)計(jì):采用多軸加工中心,精密車床、精密磨床多種設(shè)備充分結(jié)合,制定多種關(guān)鍵工序控制點(diǎn)結(jié)合的工藝流程。利用加工中心工作臺(tái)旋轉(zhuǎn)功能和原點(diǎn)轉(zhuǎn)換功能一次加工多個(gè)關(guān)聯(lián)的基準(zhǔn),并采用試切法調(diào)整零偏,為后續(xù)所有加工提供加工基準(zhǔn);同時(shí)針對(duì)SLM增材制造渦輪殼體的變形問題提出平衡裝夾力、增加輔助支撐、調(diào)整加工參數(shù)等工藝策略,解決復(fù)雜結(jié)構(gòu)精密加工難點(diǎn),滿足基于SLM增材制造渦輪殼體的微米級(jí)尺寸精度及眾多關(guān)鍵技術(shù)要求。精密加工過程見圖9。
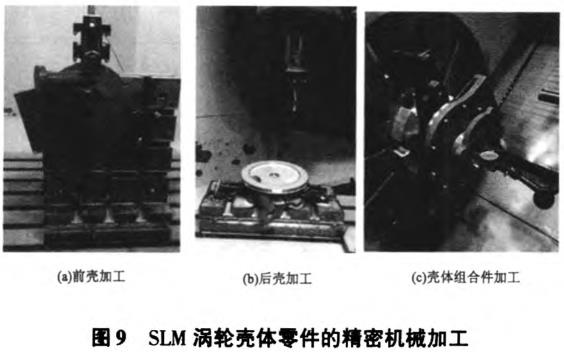
2)切削工藝的選擇及切削參數(shù)的優(yōu)化:針對(duì)SLM新型難加工材料切削過程產(chǎn)生振動(dòng)及形成較差的切削條件的特點(diǎn)。運(yùn)用防振刀桿、改制螺紋銑刀等刀具形式,同時(shí)將切削性能研究成果進(jìn)行實(shí)際應(yīng)用,針對(duì)切削加工的主要因素如切削速度、進(jìn)給速度、切削程度等,進(jìn)行切削工藝試驗(yàn)進(jìn)行切削參數(shù)的優(yōu)化,保證精度指標(biāo)。解決深盲孔加工、小螺紋孔加工、高精度偏心孔的數(shù)控加工等加工難題,為零件實(shí)現(xiàn)SLM增材制造提供應(yīng)用技術(shù)保障。
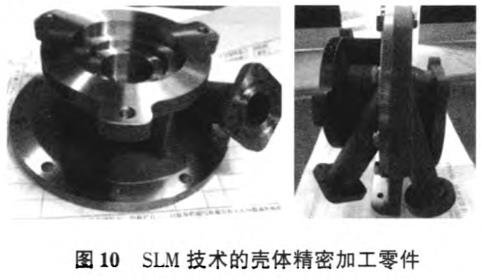
6、基于SLM技術(shù)產(chǎn)品檢測(cè)與試驗(yàn)方法研究
為了檢測(cè)產(chǎn)品性能滿足性。開展了零件三維掃描測(cè)量、化學(xué)成分和組織分析、高溫和室溫力學(xué)性能檢測(cè)、無損探傷等檢測(cè)。并根據(jù)產(chǎn)品使用要求開展地面載荷試驗(yàn)。
1)三維掃描測(cè)量技術(shù)實(shí)現(xiàn)產(chǎn)品的快速、可視化尺寸及形位質(zhì)量檢測(cè)
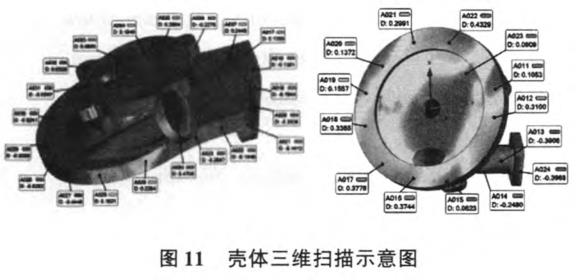
2)SLM增材制造高溫鈦合金材料的成分及理化性能檢測(cè)和評(píng)判標(biāo)準(zhǔn)研究。為新材料應(yīng)用可行性提供基礎(chǔ)數(shù)據(jù)化學(xué)成分和組織分析通過產(chǎn)品同爐試塊分析,成分檢測(cè)內(nèi)容包括:Ti、Al、Si、Zr、Mo、C、H、O、N等;高溫和室溫力學(xué)性能檢測(cè)包括抗拉強(qiáng)度、規(guī)定非比例延伸強(qiáng)度、斷后伸長(zhǎng)率、斷面收縮率等室溫力學(xué)性能檢測(cè),500℃高溫力學(xué)性能檢測(cè);著色滲透熒光檢測(cè)和x光探傷主要檢測(cè)殼體成形后的表面質(zhì)量和內(nèi)部裂紋等缺陷。
3)地面試驗(yàn)考核氣密試驗(yàn)考核產(chǎn)品結(jié)合面密封可靠度的試驗(yàn),對(duì)產(chǎn)品充氣0.6MPa。保持5min,不允許有壓降。試驗(yàn)滿足設(shè)計(jì)指標(biāo)。
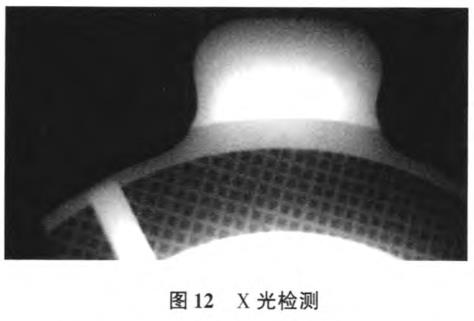
按照技術(shù)要求,產(chǎn)品在額定負(fù)載和半負(fù)載下進(jìn)行冷氣試驗(yàn),考核產(chǎn)品在冷狀態(tài)下與其它零部件的匹配性以及功能滿足性。冷氣負(fù)載試驗(yàn)結(jié)果表明性能滿足設(shè)計(jì)指標(biāo)。
7、結(jié)論
采用了基于SLM的金屬增材制造技術(shù)實(shí)現(xiàn)了結(jié)構(gòu)復(fù)雜度高、工作環(huán)境苛刻、可靠性要求高的航天關(guān)鍵零件的3D打印與精密加工。突破了基于SLM技術(shù)的功能最優(yōu)一體化、輕量化的設(shè)計(jì)技術(shù),應(yīng)用拓?fù)渚W(wǎng)狀結(jié)構(gòu),在保持結(jié)構(gòu)強(qiáng)度和剛度基本不變的條件下,減輕了零件的結(jié)構(gòu)質(zhì)量10%左右,零件生產(chǎn)周期相對(duì)于傳統(tǒng)制造工藝縮短50%以上,材料利用率由21.3%提高到達(dá)到85%以上:突破了基于SLM技術(shù)耐高溫鈦合金TC11增材制造技術(shù)應(yīng)用研究,材料性能達(dá)到材料手冊(cè)提供的物理性能指標(biāo),零件尺寸精度達(dá)到±0.1mm、表面粗糙度小于Ra6.3μm,處于國(guó)內(nèi)領(lǐng)先水平;突破了精密加工及三維檢測(cè)技術(shù),實(shí)現(xiàn)了復(fù)雜零件空間尺寸的三維在線檢測(cè),大大提升了檢測(cè)效率。產(chǎn)品通過了地面冷氣試驗(yàn)考核驗(yàn)證。
該項(xiàng)目為航天產(chǎn)品快速制造平臺(tái)構(gòu)建提供了技術(shù)支持,提供了一種高效、集約的新型設(shè)計(jì)制造方式,對(duì)提高產(chǎn)品性能、提高材料利用率、降低研制周期、節(jié)約生產(chǎn)裝配成本具有重要意義。
參考文獻(xiàn):
[1]王運(yùn)贛.三維打印自由成形[M].北京:機(jī)械工業(yè)出版社,2012.
[2]任敬心.難加工材料磨削技術(shù)[M].北京:電子工業(yè)出版社,2011.
相關(guān)鏈接