鈦合金具有高比強度、高比模量和低密度等優(yōu)異性能,在航空航天領域一直備受關注[1-2]。為了實現(xiàn)輕量化,航空發(fā)動機葉片大量采用鈦合金制造。鈦合金的硬度較低,加之發(fā)動機的工況較惡劣,難以抵御空氣中的砂粒,易在高速氣流作用下出現(xiàn)沖蝕損傷,因而沖蝕磨損成為鈦合金發(fā)動機葉片的主要失效形式之一[3-5]。以等徑角擠壓和高壓扭轉(zhuǎn)為代表的大塑性變形技術,以離子注入、金屬蒸汽真空弧技術、電弧等離子體沉積技術等為代表的表面涂層技術,是目前提高鈦合金抗沖蝕性能的常用手段。經(jīng)等徑角擠壓工藝處理后,鈦合金產(chǎn)生了均勻、細小的α相,并彌散在β相內(nèi),可有效提高鈦合金的強韌性[6],對砂粒起到了切向攔截作用,從而減小了微切削造成的破壞,沖蝕損傷機理發(fā)生改變,最終提升了鈦合金的抗沖蝕能力。通過表面涂層技術制備不同結(jié)構的TiAlN/Ti[7]、TiZrN[8]、CrSiN/Cr[9],可以提高鈦合金的抗沖蝕性能,進而提升發(fā)動機葉片的服役年限。
在沖蝕過程中,材料與工藝因素的交互作用使得磨料特性和沖蝕工藝參數(shù)對基材損傷過程的影響非常復雜,鈦合金沖蝕損傷過程既存在對砂塵粒徑的依賴效應[10],又存在基于沖蝕角度的機理演變效應[11]。
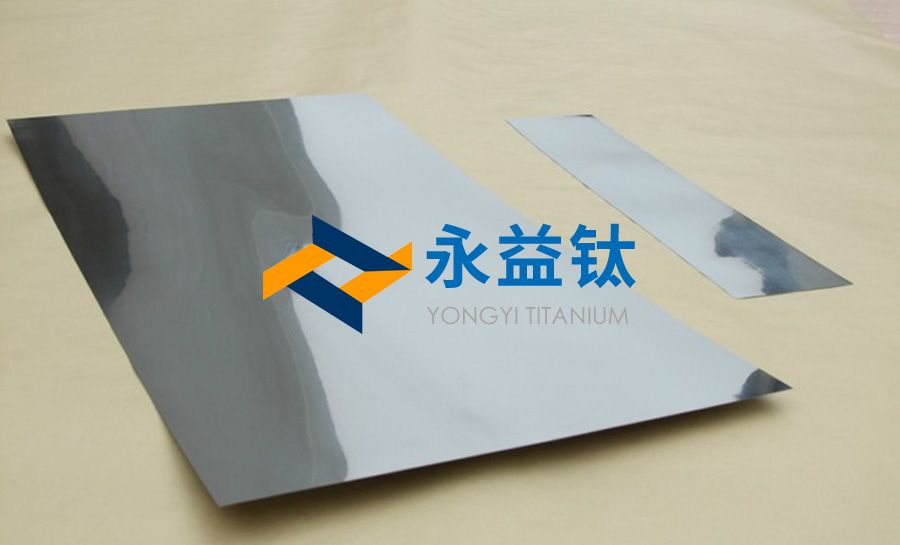
李超等[12]通過實驗和數(shù)值模擬,研究了砂粒粒徑對渦軸發(fā)動機壓氣機葉片TC4鈦合金沖蝕磨損的影響,結(jié)果表明,砂粒粒徑與沖擊速度存在內(nèi)在關聯(lián),粒徑越大,則沖擊速度越小。葉片沖蝕磨損率與砂粒沖擊速度呈冪函數(shù)關系。不同粒徑的砂粒對不同葉高處的磨損率濃度的敏感程度存在顯著差異,此研究結(jié)果為葉片抗磨損設計提供了理論依據(jù)。Avcu等[13]從沖蝕角度、沖擊速度和顆粒尺寸等方面考察了Ti6Al4V鈦合金的沖蝕磨損行為,發(fā)現(xiàn)沖蝕率與沖蝕速度成正比,與沖蝕顆粒尺寸成反比。無論沖蝕顆粒直徑如何變化,最大沖蝕率總是出現(xiàn)在30°攻角附近。沖蝕速度和顆粒尺寸會影響鈦合金的沖蝕損傷程度,但不影響其沖蝕機制,沖蝕機制以微切削和塑性變形為主,在基材表面均檢測到侵蝕粒子。Sahoo等[14]研究了Ti6Al4V鈦合金在層狀、雙峰、等軸3種不同微觀結(jié)構下的固體顆粒沖蝕行為,發(fā)現(xiàn)層狀結(jié)構組織的鈦合金沖蝕率最小,其次是雙峰和等軸結(jié)構,這主要歸因于不同微觀組織下硬度的不同。Guo[15]研究了30°、60°、90°攻角下的TC4鈦合金沖蝕機理,發(fā)現(xiàn)隨著攻角的增加,沖蝕率逐漸減小。在30°攻角下,沖蝕率約為90°攻角下的2倍。在低角度沖蝕下,主要的破壞形式為微切削和犁削,在90°攻角下主要為疲勞破壞。李巾杰等[16]研究發(fā)現(xiàn),隨著沖蝕時間的延長,鈦合金表面沖蝕坑的深度逐漸增加,沖蝕損傷特征從30s時的變形唇和微切削,演變成120s時的塑性疲勞剝落。吳松波等[17]分析了磨料粒徑和沖蝕次數(shù)對TC4鈦合金沖蝕磨損行為的影響,研究發(fā)現(xiàn),隨著磨料粒徑的增加,磨損面積和磨損深度呈現(xiàn)先增加后減小趨勢;沖蝕次數(shù)與磨損體積呈顯著正相關,磨損機制主要表現(xiàn)為磨料棱角對基體的微切削和擠壓剝落。
Yan等[18]綜合考慮了粒度、速度和磨料破裂等因素,建立了鈦合金葉片材料的沖蝕率預測模型,獲得了磨料破裂判據(jù),并量化了磨料破碎對侵蝕的影響。作者還發(fā)現(xiàn),同種材料在不同沖蝕速度下最大沖蝕率對應的攻角不同,在一定速度區(qū)間內(nèi),高速沖蝕時最大沖蝕率對應的攻角大于低速沖蝕時,這也解釋了不同文獻中TC4鈦合金最大沖蝕率對應的攻角不同,在30°、40°、45°時均有可能出現(xiàn)的原因。
目前,文獻中大都采用30°、45°、60°、90°等特殊攻角,研究鈦合金的抗沖蝕性能,采用小角度間隔探求攻角的影響規(guī)律的研究較少。采用控制變量法研究單一因素對沖蝕損傷影響的文獻較多,但采用正交試驗法探索工藝因素影響沖蝕主次關系的報道較少。
基于此,文中采用正交試驗聯(lián)合控制變量法研究沖蝕工藝參數(shù)對鈦合金沖蝕損傷的影響,結(jié)合數(shù)值模擬,共同揭示沖蝕機理的演變規(guī)律,旨在為鈦合金構件的抗沖蝕設計提供理論參考。
1、實驗
1.1材料
沖蝕基材采用陜西寶雞中寶泰金屬有限公司生產(chǎn)的厚度為5mm的退火態(tài)TC4鈦合金板,元素組成(均用質(zhì)量分數(shù)表示):Al6.0%、V4.0%、Fe0.3%、C0.08%、N0.05%、H0.015%、O0.2%,其余為Ti。采用線切割切成16mm×23mm×5mm的樣品,統(tǒng)一打磨拋光所有的待沖蝕表面。在實驗前后,均用酒精超聲清洗樣品5min,并烘干。沖蝕磨料采用鄭州越馳磨料磨具有限公司生產(chǎn)的60目白剛玉,其顯微硬度約為20GPa。磨料的微觀形貌及X射線衍射圖譜如圖1所示,可以看出,磨料的形狀不規(guī)則,邊緣尖銳,其主要成分為高硬度的Al2O3,還有少量的SiO2。
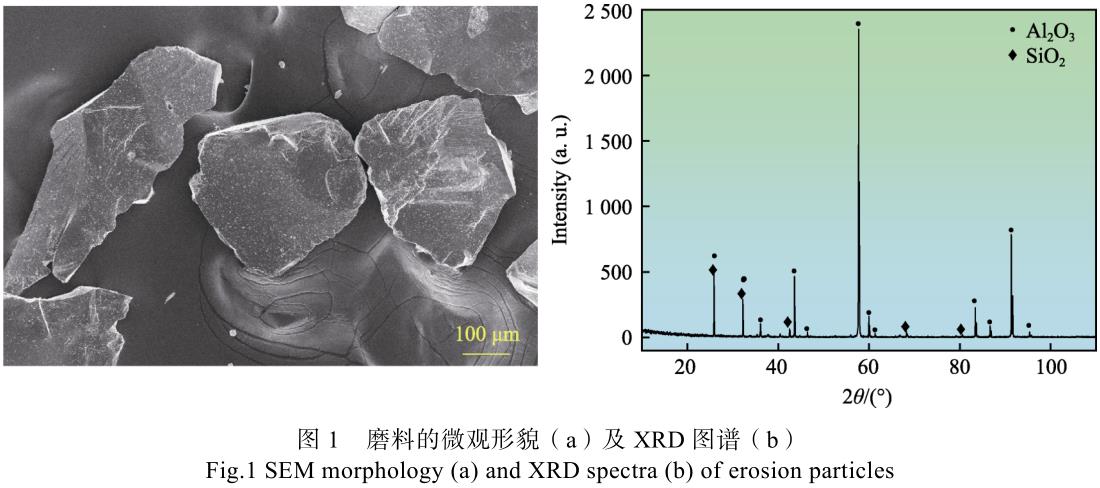
1.2材料表征
采用美國FEI公司的Quanta250型掃描電鏡和EDAX能譜儀表征磨料和沖蝕前后鈦合金的微觀形貌和元素組成。采用德國布魯克D8AdvanceX射線衍射儀檢測磨料的物相。采用Cu-Kα輻射(0.15406nm),掃描范圍為10°~110°,掃描步長為10(°)/min。采用精度為0.1mg的FA1604型電子天平表征沖蝕量(E,mg),單個試樣均測量3次,取其平均值。
1.3沖蝕試驗設計
采用自行研制的常溫沖蝕試驗機進行沖蝕試驗,原理如圖2所示[19]。選用L9(34)正交表設計試驗(表1),試驗因素分別為沖蝕距離(A,mm)、沖蝕角度(B,(°))和沖砂量(C,g),忽略因素間交互作用的影響??刂谱兞吭囼瀰?shù):沖蝕距離為90mm;沖砂量為200g;沖蝕角度,低攻角分別為15°、30°、35°,中攻角分別為40°、45°、50°,高攻角分別為60°、75°、90°;沖蝕壓力約為0.6MPa。
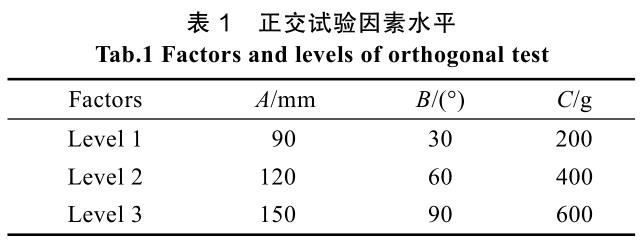
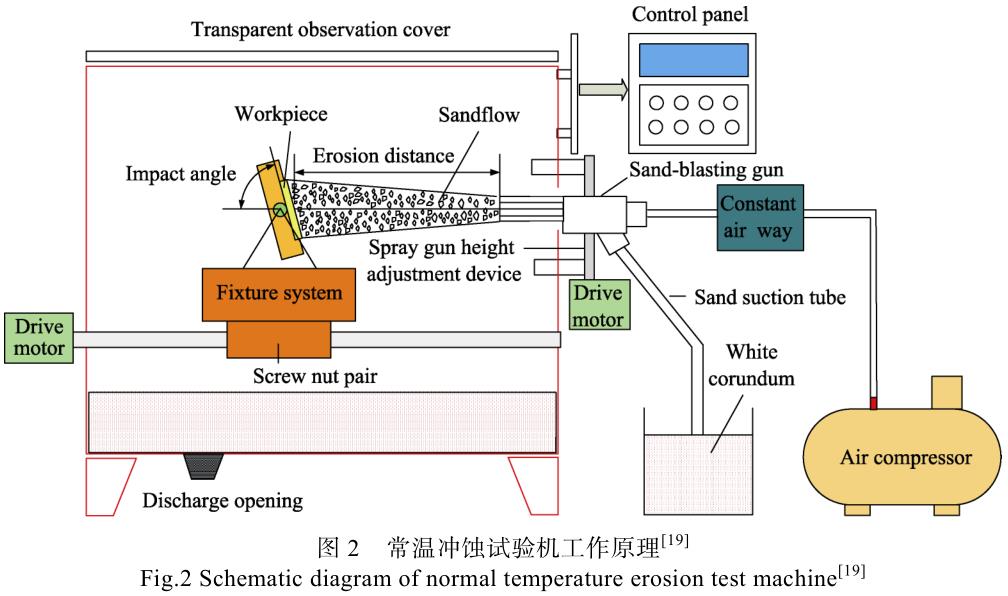
2、結(jié)果與討論
2.1正交試驗結(jié)果與分析
極差R可以直觀反映試驗因素對沖蝕率的影響程度。沖蝕量(E)的極差分析見表2,可以看出,沖蝕量受到?jīng)_蝕距離的影響程度最大,沖砂量次之,沖蝕角度最小,且沖蝕量最大和最小時的試驗因素組合分別為A1B2C3、A3B1C1,此結(jié)果可為結(jié)構件沖蝕環(huán)境參數(shù)的設計提供理論參考。
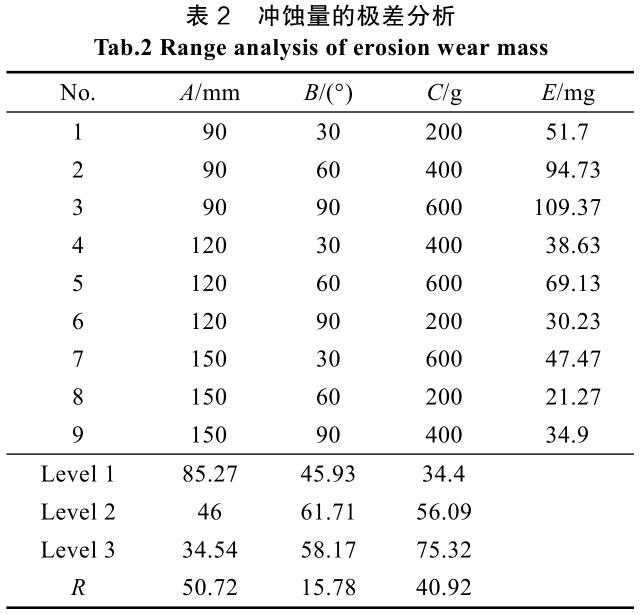
沖蝕量隨因素水平變化的趨勢如圖3所示,可見,當沖蝕距離從90mm逐漸增至150mm時,沖蝕量急劇下降。這是由于沖蝕距離的增大,導致磨料動能損失增大,到達靶材時的撞擊力隨之減小,靶材的損傷程度減輕。沖蝕量隨著沖蝕角度的增加呈先增大后減小的趨勢。這是因為在小角度沖蝕時靶材的損傷形式以犁削、切削為主,而在高角度沖蝕時以撞擊和塑性變形為主,使得材料的去除率反而降低,這主要由于沖蝕損傷機理發(fā)生改變。沖砂量與沖蝕量基本呈正相關,沖砂量的增加表示沖蝕時間延長。在沖蝕初期,靶材表面較為光滑,飛行磨料難以切削,甚至反彈。隨著沖蝕時間的延長,靶材表面開始毛化,變得粗糙,粒子切削變得相對容易,沖蝕量逐漸增大,加之沖蝕后期沖蝕機理可能發(fā)生改變,導致質(zhì)量損失更大[16]。
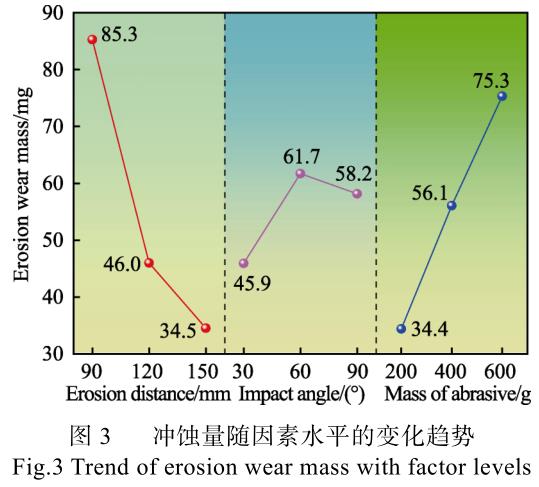
采用Minitab17.0軟件進行多因素方差分析,進而判斷各因素影響沖蝕量的顯著程度。采用一般線性模型,顯著性水平取值為0.05,不考慮因素間交互作用的影響,結(jié)果見表3。通過方差分析統(tǒng)計量F可判斷各因素影響沖蝕率的顯著性,可以看出在現(xiàn)有試驗條件下,沖蝕距離和沖砂量對沖蝕率均有顯著影響,沖蝕角度的影響并不顯著,此結(jié)果與上述極差分析結(jié)果一致。
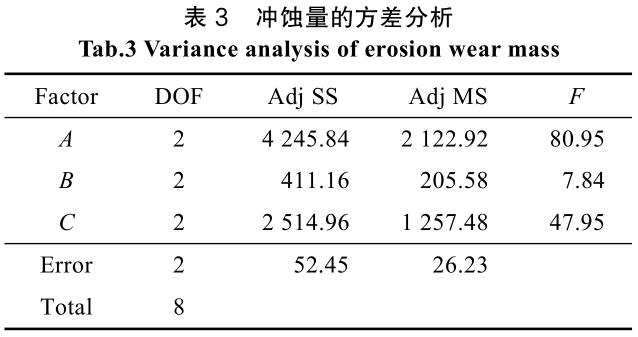
雖然正交試驗能夠分析因素對指標的影響規(guī)律,但存在水平間隔較大的缺點,且易漏掉突變值。雖然沖蝕角度對沖蝕量的影響并不顯著,但根據(jù)既有文獻發(fā)現(xiàn),沖蝕角度對沖蝕機理的影響較大[11,18]。為了深入研究鈦合金的沖蝕損傷行為,選擇沖蝕角度進行控制變量試驗。
2.2控制變量試驗結(jié)果與分析
在不同沖蝕角度下,鈦合金的沖蝕量如圖4所示。可以看出,隨著沖蝕角度的增加,沖蝕量呈現(xiàn)先增大后減小趨勢,在15°時最小,在40°時達到最大值。這與Avcu等[13]、Wang等[20]諸多學者研究的趨勢相同,只是兩者的最大沖蝕損傷峰值分別出現(xiàn)在30°、45°附近。分析認為,上述文獻并未考慮40°沖蝕角度;沖蝕損傷對磨料沖蝕速度具有依賴效應,即相同材料在不同沖蝕速度下沖蝕損傷峰值對應的攻角不同。如果磨料速度較低,則微切削占主導。如果磨料速度較高,則由微切削和錘擊效應共同主導,材料剝落較多,最大沖蝕角度出現(xiàn)了遲滯現(xiàn)象。
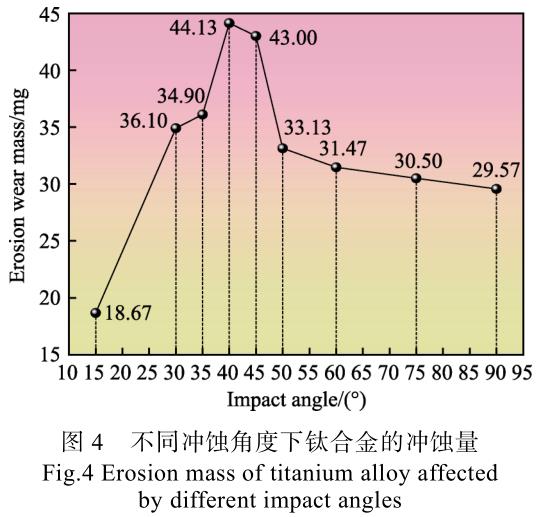
2.3基于有限元模擬的沖蝕損傷行為分析基于ABAQUS平臺的Explicit模塊,采用Johnson-Cook本構模型和損傷模型定義鈦合金材料屬性[21-22],開展鈦合金沖蝕損傷行為數(shù)值模擬。沖蝕有限元模型如圖5所示,分別在30°、45°、90°沖蝕角度下進行沖蝕損傷模擬。綜合考慮沖蝕壓力、粒子平均粒徑,忽略空氣阻力,假定粒子速度為300m/s[18],沖蝕距離設定為90mm。綜合考慮計算時間和精度,忽略沖蝕粒子的變形,基于自由網(wǎng)格劃分技術,采用四節(jié)點四面體C3D4實體單元劃分粒子網(wǎng)格,網(wǎng)格尺寸為
0.1mm。考慮基體塑性大變形,采用八節(jié)點六面體C3D8R單元劃分基體網(wǎng)格,網(wǎng)格尺寸為0.0025mm。在不同攻角下,鈦合金沖蝕截面的形貌如圖6所示。由圖6a看出,在30°攻角時,材料主要受到切削作用,在試樣表面形成了較長的犁溝,材料被擠壓至犁溝前方和兩側(cè),形成擠壓唇,且犁溝前方的擠壓唇更加明顯,更易斷裂,形成切屑,從而離開試樣表面。在犁溝內(nèi),材料在切削的作用下發(fā)生了劇烈的塑性形變,導致應力集中,當應力大于材料的屈服強度時,單元失效,材料發(fā)生大變形,并向犁溝前方塑性流動,
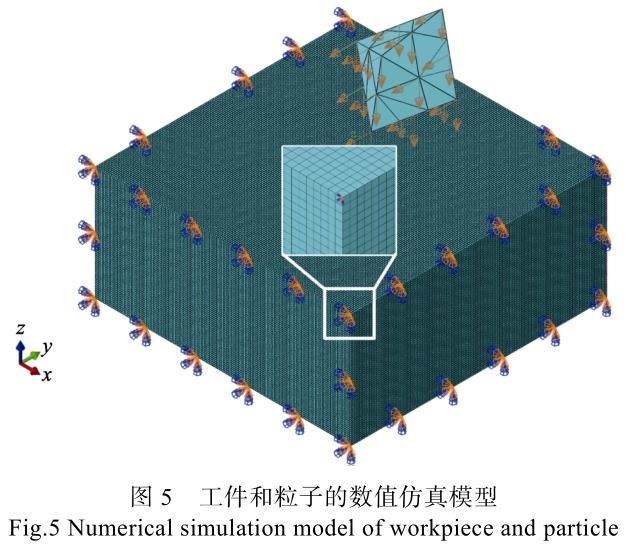
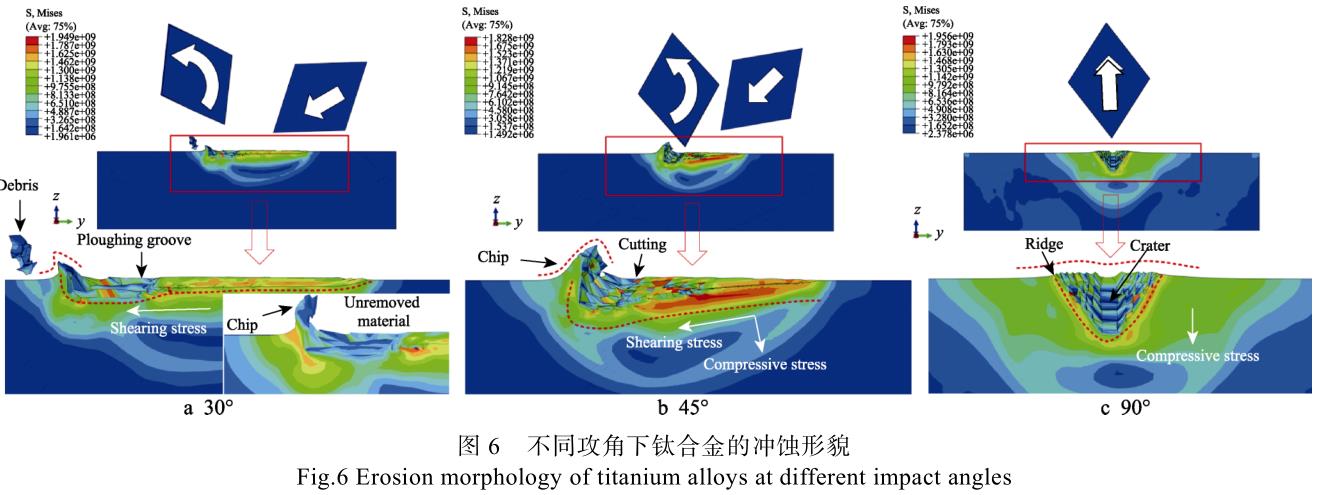
形成凸起。由圖6b看出,當攻角增至45°時,切削作用減弱,錘擊作用增強,導致切削溝槽長度減小,深度增加,擠壓唇的體積明顯增大。材料在切應力和壓應力的聯(lián)合作用下產(chǎn)生了大變形和塑性流動,損傷程度加劇。由圖6c看出,在90°攻角時,材料只受到錘擊擠壓作用,在垂直于材料表面方向發(fā)生了明顯的塑性變形,產(chǎn)生了凹坑,且材料在凹坑周圍堆積,形成脊。由仿真分析結(jié)果可知,在低角度下材料主要受到犁削、切削作用,在高角度下受到錘擊、擠壓作用,在中角度下受到切削與錘擊的聯(lián)合作用。切屑的形成
是材料質(zhì)量損失的直接原因,相較于30°時單個粒子沖蝕時便產(chǎn)生切屑,在45°攻角時較小的切削作用無法使變形唇與試樣表面分離,需在后續(xù)多個粒子沖蝕后形成切屑,而在90°時無切削作用,沖蝕機理改變,需結(jié)合試驗結(jié)果具體分析。
粒子應力變化時間歷程曲線和粒子動能時間歷程曲線如圖7~8所示??梢钥闯?,在低攻角時,錘擊作用較小,粒子受到的反作用力較小,導致應力變化和動能損失較小,粒子最終以較高速度旋轉(zhuǎn),從而離開試樣表面,如圖6a所示。在45°攻角時,錘擊作用增大,粒子受到的反作用力增大,動能損失增多,但最終運動狀態(tài)與30°攻角時一致,如圖6b所示。在90°攻角時,粒子受到的反作用力最大、動能損失最多,最終粒子沿入射軌跡平動,從而離開試樣表面。相較于90°攻角時粒子的垂直撞擊,在30°、45°攻角時粒子斜向侵入材料,與試樣的接觸面積較大,因此容易發(fā)生二次撞擊,接觸時間較長,導致粒子的受力曲線出現(xiàn)了2次峰值。在90°時,粒子僅發(fā)生1次撞擊后便反彈離開。由圖8可以看出,相較于攻角30°,在攻角45°、90°時粒子的動能損失較大。
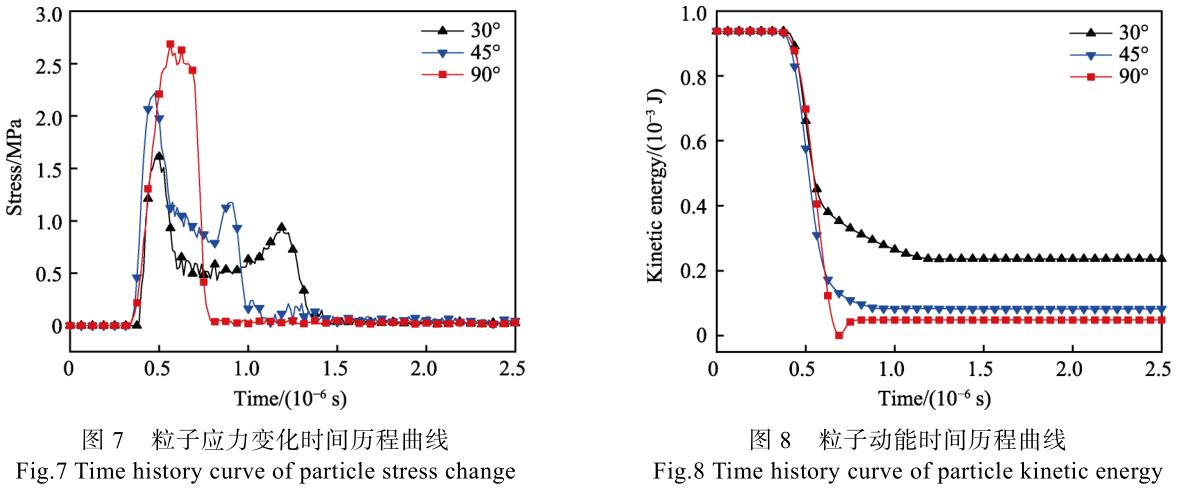
2.4沖蝕機理分析
在不同攻角下,鈦合金的沖蝕表面形貌如圖9所示。由圖9a可以看出,在低攻角時,材料表面分布著大量的犁溝和擠壓唇,犁溝方向與沖蝕方向一致,流動性較明顯。磨料的硬度遠大于鈦合金的硬度,導致鈦合金在磨粒高速撞擊下極易發(fā)生塑性變形。由于犁溝寬度遠小于磨料尺寸(約290μm),且在低攻角下磨料的速度水平分量較大,因此材料主要受到小部分磨料(尖角)的切削作用,向兩側(cè)移動,并堆積形成擠壓唇,在與磨粒直接接觸的區(qū)域形成較長犁溝,符合塑性材料微切削理論。變形唇在后續(xù)粒子切削、擠壓的作用下產(chǎn)生循環(huán)應力后被去除,僅剩下犁溝分布在材料表面。如圖9b所示,材料在磨料尖角的作用下產(chǎn)生了劃痕,由損傷界線可以看出,多次切削導致材料被大面積去除。由圖9c可以看出,在中攻角時,材料表面沿著沖蝕方向存在犁溝和切削痕跡,同時出現(xiàn)了少量凹坑。由變形磨損理論可知,攻角的增大導致磨粒的速度垂直分量增大,錘擊作用增強,侵入深度增加。可以看出,在中攻角下犁溝的長度相較于低攻角(圖9a)時減小,但其損傷程度明顯增加;較多材料受到切削作用,沿磨料運動方向移動,并堆積在磨料離開的位置,出現(xiàn)隆起,形成了明顯的脊,脊的體積大于低攻角下擠壓唇的體積,且在脊的后方形成了切削痕跡;在少量磨料的錘擊作用下,形成了凹坑,材料被擠出凹坑,并在四周凸起。由圖9d可以看出,在中攻角下劃痕區(qū)域的損傷程度明顯大于低攻角下(圖9b),這與圖9a、c所示的損傷程度一致。
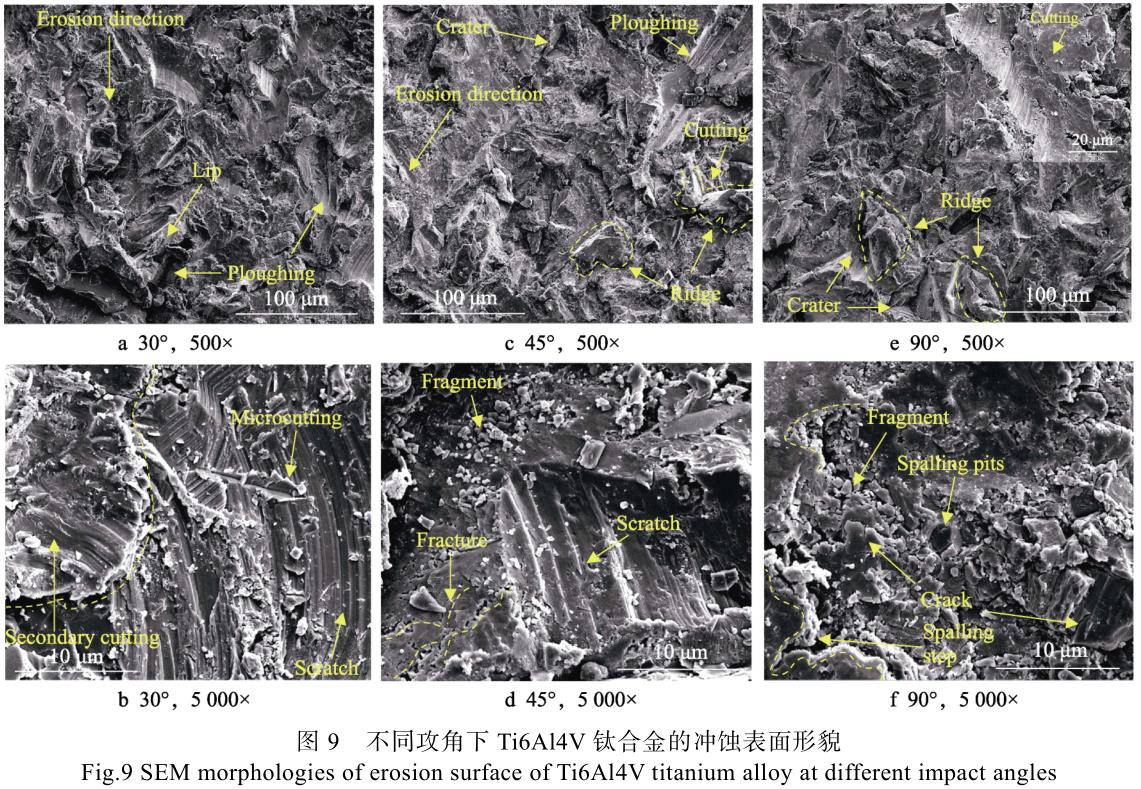
錘擊作用的增強,導致材料萌生裂紋,大量裂紋交匯后,在后續(xù)粒子的持續(xù)作用下形成了碎片,并脫落。在切削與錘擊的聯(lián)合作用下產(chǎn)生的多種損傷形式是鈦合金在中攻角時沖蝕量較高的原因。由圖9e可以看出,在高攻角時,材料表面存在方向性不明顯的凹坑、脊及少量切削痕跡,此時材料只受到錘擊作用。
由鍛造擠壓理論可知,材料在磨粒正向錘擊作用下會產(chǎn)生凹坑和凸起的脊,脊在后續(xù)磨粒的反復擠壓、鍛打下會發(fā)生加工硬化和韌脆轉(zhuǎn)變[10],從而加速裂紋的形成,之后擴展并斷裂,生成碎片,其數(shù)量相較于中攻角時明顯增多,碎片脫落,形成了大尺寸的剝落臺階和小尺寸的剝落坑(圖9f)。隨著攻角的增大,入射軌跡與反彈軌跡重合的程度增大。在高攻角時,2條軌跡基本重合,較多磨粒發(fā)生碰撞,導致入射磨粒的原始軌跡發(fā)生偏轉(zhuǎn),攻角減小,產(chǎn)生切削作用。由于存在發(fā)散角,導致攻角改變,同樣會產(chǎn)生切削作用,因此在高攻角下沖蝕表面存在少量切削痕跡。
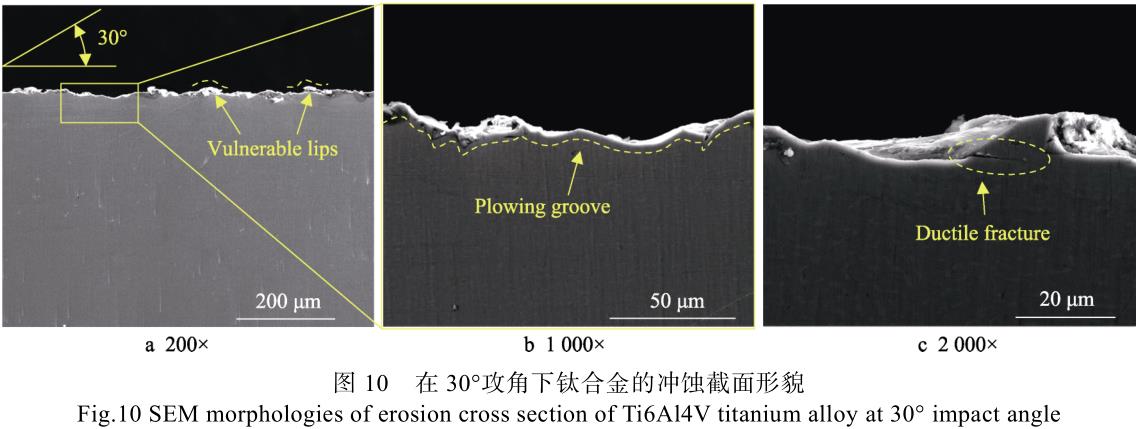
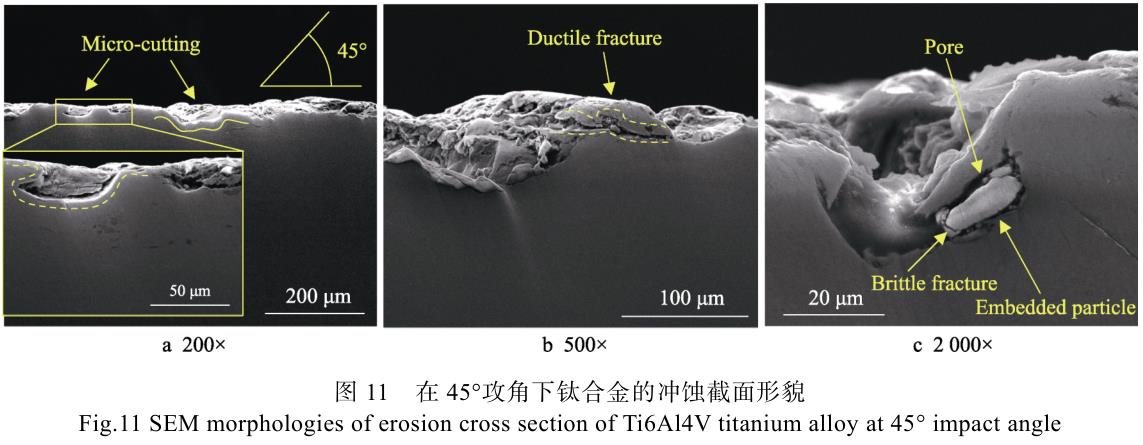
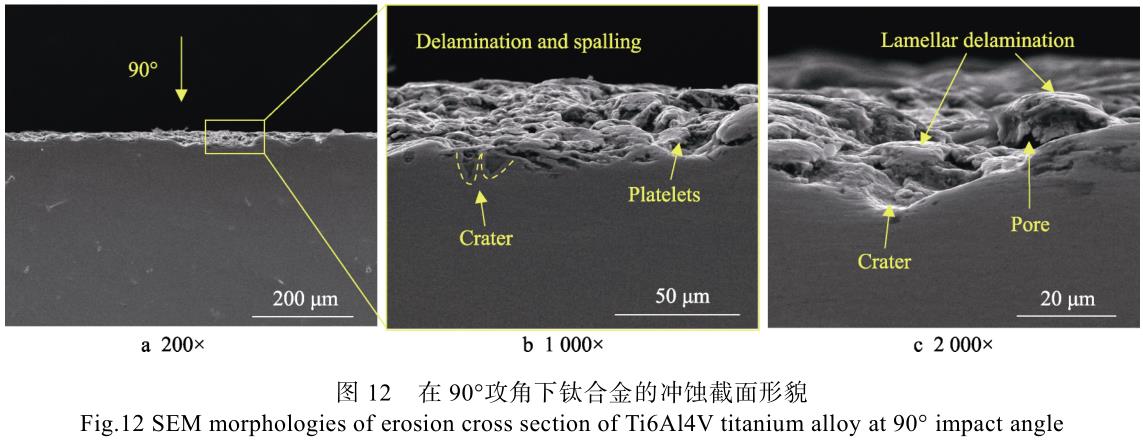
在不同攻角下,鈦合金沖蝕截面形貌如圖10~12所示。由圖10a、b可以看出,在低攻角時,磨料的速度水平分量遠大于垂直分量,使得切削作用遠大于錘擊作用,導致犁溝的長度遠大于深度,且擠壓唇分布于犁溝前端,呈現(xiàn)出凹凸不平的波狀形貌。如圖10c所示,同一位置的材料受到多個磨粒的切削作用,達到屈服極限,從而萌生裂紋,在隨后磨粒的撞擊下沿水平方向擴展成橫向裂紋,材料出現(xiàn)脫落,形成犁溝。由圖11a、b可以看出,在中攻角時,切削作用減小,導致溝槽長度減小,錘擊力增加,磨粒的侵入深度增加,橫向裂紋出現(xiàn)在更深位置,導致切削溝槽深度大于犁溝深度,去除材料的體積更大。同時,錘擊力的增加使得粒子受到的反作用力增大,更易發(fā)生脆性斷裂,并嵌入材料內(nèi)部(圖11c)。磨粒碎片在后續(xù)磨粒的撞擊下發(fā)生了脆斷和松動,產(chǎn)生了裂紋、碎片、孔隙,侵入深度進一步增加。如圖12所示,在高攻角時,材料表面在正向錘擊作用力下產(chǎn)生了凹坑,同時材料被擠壓至凹坑四周,形成了脊。在磨粒的反復鍛打下,脊向凹坑處塑性流動、鋪展、壓平后,形成了極薄的唇片,如圖12b所示。唇片在凹坑處相互擠壓、搭接,未能完全填充凹坑,形成的層狀結(jié)構中的孔隙使得沖蝕區(qū)域疏松多孔,其表面凹凸不平程度顯著增大,材料的強度下降,如圖12c所示。在后續(xù)磨粒的反復作用下,唇片出現(xiàn)疲勞斷裂、分層剝落,形成臺階狀沖蝕區(qū),反而使沖蝕凹坑深度相較于中攻角時有所減?。▓D11a),但正向錘擊作用下產(chǎn)生的凹坑深度明顯大于低攻角時犁溝的深度(圖10a)。
通過上述分析可知,在低攻角下,鈦合金的沖蝕損傷主要為犁削、切削作用導致的犁溝、切削痕跡、擠壓唇和橫向裂紋;在中攻角下,沖蝕損傷表現(xiàn)為切削與錘擊聯(lián)合作用下產(chǎn)生的多種破壞形式,如更深的犁溝、更高的脊(擠壓唇)、更深的橫向裂紋和沖擊碎片;在高攻角下,材料表面在正向錘擊、鍛打作用下出現(xiàn)加工硬化、韌脆轉(zhuǎn)變、疲勞斷裂和分層剝落,材料表面碎片化程度更為嚴重。在中攻角下,多種沖蝕損傷形式的疊加使得其沖蝕量大于其他攻角下的單一沖蝕損傷。
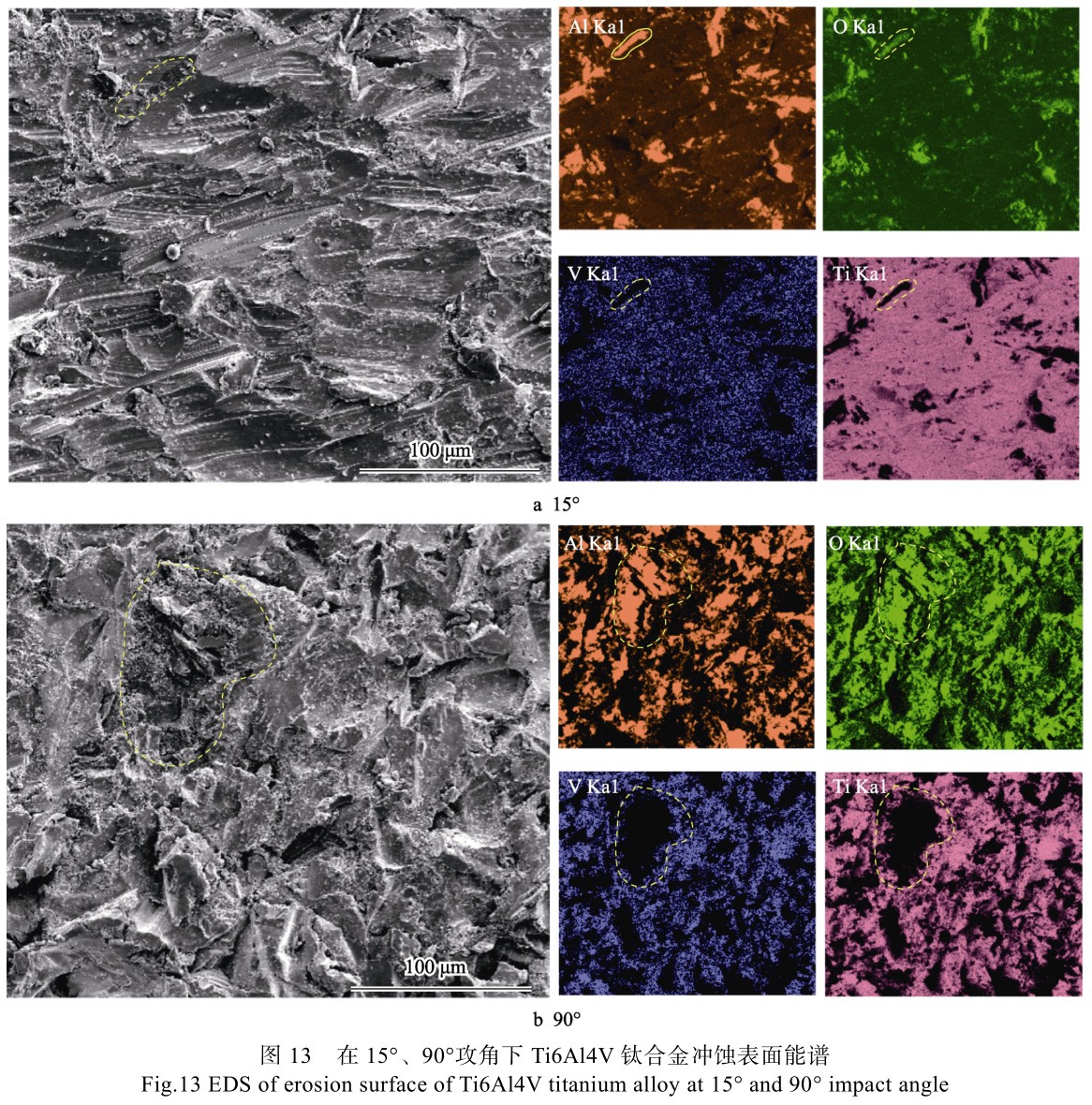
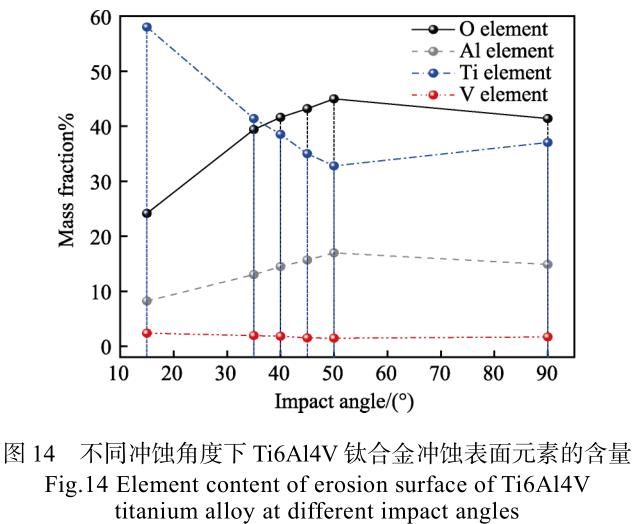
在低、高攻角下,鈦合金沖蝕表面能譜分析結(jié)果如圖13所示??梢钥闯觯?種工況下,材料表面沖蝕損傷區(qū)域中的Ti、V元素含量明顯減少,且該區(qū)域出現(xiàn)了Al、O元素,表明材料在被去除的同時出現(xiàn)了磨粒破碎并嵌入的現(xiàn)象。在不同攻角下,鈦合金沖蝕表面元素含量如圖14所示,可知在低攻角下鈦合金元素的含量最高,在高攻角下次之,在中攻角下最低。磨料元素的變化規(guī)律與其相反,二者與沖蝕量變化規(guī)律一致。即沖蝕量越高,則材料去除量越大,同時嵌入的粒子越多;沖蝕量越低,則反之。結(jié)合上述分析可知,在低攻角時磨料受到的反作用力較?。▓D7),較少的磨粒破碎[23];原始磨料的尺寸較大,動能較大,不易被塑性材料橫向拖曳并嵌入材料,反而以低入射角度侵入材料表層,并輕易去除材料,之后以較小反射角離開材料表面,且反彈軌跡與入射軌跡的重合程度較?。▓D6a),因碰撞而破碎的磨粒數(shù)量更少,導致低攻角下材料表面磨料的元素較少。在中攻角時,磨粒受到的反作用力增大(圖7),破碎數(shù)量增多,同時入射軌跡與反射軌跡的重合程度增大,導致碰撞破碎的可能性增加;侵入深度的增加,使得破碎磨粒被較多材料拖曳,運動阻力增大,嵌入材料的可能性增加。在以上因素的綜合作用下,沖蝕表面磨粒的元素最多。通過上述分析可知,在高攻角時,粒子破碎的數(shù)量較多,侵入深度進一步增加,使得磨粒的嵌入數(shù)量較多。此時磨粒受到的反作用力增加,導致反彈磨粒的數(shù)量增多,且入射軌跡與反彈軌跡高度重合(圖6c),使得反彈后磨粒與后續(xù)磨粒劇烈碰撞,磨粒動能減小,反而在一定程度上減輕了嵌入程度,因此在高攻角下磨粒元素的含量略低于中攻角下。
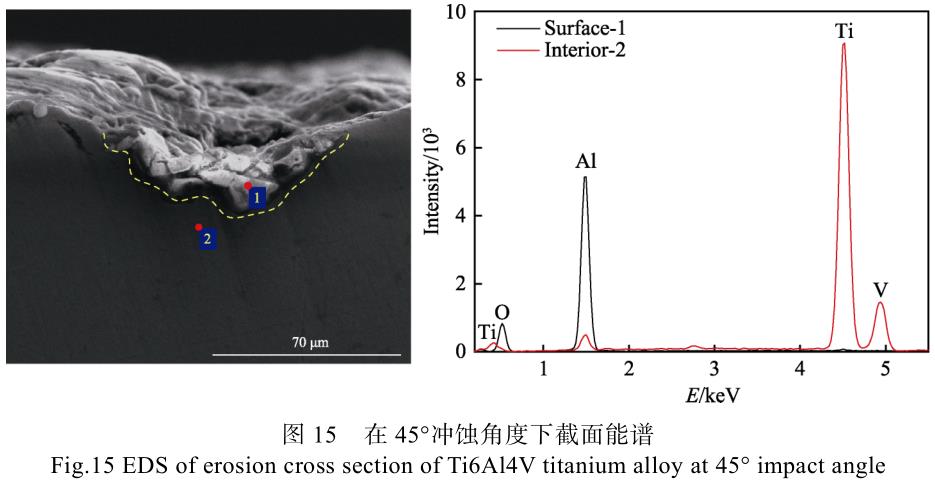
沖蝕截面(中攻角)能譜分析結(jié)果如圖15所示,可以看出,在材料表面沖蝕區(qū)域內(nèi)磨粒元素(Al、O)的含量遠大于材料內(nèi)部,且白色顆粒會發(fā)生脆性斷裂,生成的碎片嵌入坑內(nèi),碎片與材料的界限清晰。結(jié)合圖13、14可斷定,在各個攻角下,磨粒均破碎,并嵌入基體。
3、結(jié)論
1)鈦合金表面沖蝕損傷的影響因素依次為沖蝕距離、沖砂量、沖蝕角度。在沖蝕距離為90mm、沖砂量為200g、沖蝕壓力約為0.6MPa的工況下,鈦合金的最大沖蝕損失出現(xiàn)在沖蝕角度40°附近。
2)沖蝕損傷過程模擬結(jié)果表明,在低攻角到高攻角的沖蝕過程中,由切削作用占主導,逐步演變?yōu)殄N擊作用占主導。在低角度下沖蝕時,磨料容易發(fā)生二次切削。在高角度下沖蝕時,磨料撞擊后會反彈離開。沖蝕角度越大,則磨料的動能損失越大。
3)沖蝕機理與沖蝕角度密切相關。在低攻角下,鈦合金的沖蝕損傷主要表現(xiàn)為犁削和微切削導致的犁溝、擠壓唇和橫向裂紋;在高攻角下,沖蝕損傷主要表現(xiàn)為正向錘擊、鍛打作用引起的加工硬化、韌脆轉(zhuǎn)變、疲勞斷裂和分層剝落。
參考文獻:
[1]ZHAO S, MENG F Y, FAN B L, et al. Evaluation of Wear Mechanism between TC4 Titanium Alloys and Self-Lu-bricating Fabrics[J]. Wear, 2023, 512: 204532.
[2]HERRERA P, HERNANDEZ-NAVA E, THORNTON R,et al. Abrasive Wear Resistance of Ti-6AL-4V Obtained by the Conventional Manufacturing Process and by Elec-tron Beam Melting (EBM)[J]. Wear, 2023, 524: 204879.
[3]王彥峰, 李爭顯, 杜繼紅, 等. TC4 鈦合金表面滲碳復合 TiN(Ti)膜層的抗沖蝕性能[J]. 稀有金屬材料與工程,2019, 48(6): 1878-1883.
WANG Y F, LI Z X, DU J H, et al. Solid Particle Erosion of Composite Coating of Gradient Carburized Layer and TiN (Ti) Coating Synthesized on TC4 Alloy[J]. Rare Metal Materials and Engineering, 2019, 48(6): 1878-1883.
[4]BIN G F, LI C, LI J, et al. Erosion-Damage-Induced Vibration Response of Aero-Gas Generator Rotor System[J].Mechanical Systems and Signal Processing, 2023, 195:110298.
[5]RUAN H T, WANG Z Y, WANG L, et al. Designed Ti/TiN Sub-Layers Suppressing the Crack and Erosion of TiAlN Coatings[J]. Surface and Coatings Technology,2022, 438: 128419.
[6]李振華, 華晨, 程先華. 等徑角擠壓后Ti5553鈦合金的沖蝕磨損機理演變[J]. 摩擦學學報, 2015, 35(1): 45-52.
LI Z H, HUA C, CHENG X H. Erosion Mechanism Evolution of Ti5553 Treated by Equal Channel Angular Extrusion[J]. Tribology, 2015, 35(1): 45-52.
[7]李玉琴, 文建中, 孫志平. TC4 鈦合金表面 TiAlN/Ti 涂層的抗沖蝕性能研究[J]. 表面技術, 2021, 50(7): 276-282.
LI Y Q, WEN J Z, SUN Z P. Study on Erosion Resistance of the TiAlN/Ti Coating for TC4 Titanium Alloy[J]. Surface Technology, 2021, 50(7): 276-282.
[8]MA A M, LIU D X, ZHANG X H, et al. Solid Particle Erosion Behavior and Failure Mechanism of TiZrN Coatings for Ti-6Al-4V Alloy[J]. Surface and Coatings Technology, 2021, 426: 127701.
[9]CAI F, ZHANG J M, WANG J M, et al. Improved Adhesion and Erosion Wear Performance of CrSiN/Cr Multi-Layer Coatings on Ti Alloy by Inserting Ductile Cr Layers[J]. Tribology International, 2021, 153: 106657.
[10]耿明睿, 陳皎, 楊竹芳, 等. TC4 鈦合金表面沖蝕損傷機理的砂塵粒徑依賴效應[J]. 中國表面工程, 2018,31(3): 17-26.
GENG M R, CHEN J, YANG Z F, et al. Dependent Effects of Particle Size on Erosion Wear Mechanism of TC4 Titanium Alloy[J]. China Surface Engineering, 2018,31(3): 17-26.
[11]KHODDAMI A, SALIMI-MAJD D, MOHAMMADI B.Finite Element and Experimental Investigation of Multi-ple Solid Particle Erosion on Ti-6Al-4V Titanium Alloy
Coated by Multilayer Wear-Resistant Coating[J]. Surface and Coatings Technology, 2019, 372: 173-189.
[12]李超, 賓光富, 李堅, 等. 砂粒粒徑對航空渦軸發(fā)動機壓氣機葉片沖蝕磨損的影響研究[J]. 機械工程學報,2022, 58(19): 180-190.
LI C, BIN G F, LI J, et al. Influence of Sand Particle Size on the Erosive Wear of Compressor Blade in an Aero-Turboshaft Engine[J]. Journal of Mechanical Engineering,2022, 58(19): 180-190.
[13]AVCU E, FIDAN S, YLDRAN Y, et al. Solid Particle Erosion Behaviour of Ti6Al4V Alloy[J]. Tribology -Materials, Surfaces & Interfaces, 2013, 7(4): 201-210.
[14]SAHOO R, MANTRY S, SAHOO T K, et al. Effect of Microstructural Variation on Erosion Wear Behavior of Ti-6Al-4V Alloy[J]. Tribology Transactions, 2013, 56(4):555-560.
[15]GUO B H. Research on Solid Particle Erosion Behaviors of TC4 Alloy at Different Erosion Angles[J]. Advanced Materials Research, 2014, 1049/1050: 167-170.
[16]李巾杰, 吳鳳芳, 吳冰. 鈦合金基體上 AlCrN 涂層的沖蝕磨損行為研究[J]. 表面技術, 2019, 48(2): 152-158.
LI J J, WU F F, WU B. Erosion Wear Performance of AlCrN Coating on Titanium Alloy Substrate[J]. Surface Technology, 2019, 48(2): 152-158.
[17]吳松波, 蔡振兵, 林禹, 等. 硬質(zhì)沙粒對 TC4 鈦合金沖擊磨損的損傷行為的研究[J]. 摩擦學學報, 2018, 38(4):383-390.
WU S B, CAI Z B, LIN Y, et al. Effect of Hard Sand on the Impact Wear Behavior of TC4 Alloy[J]. Tribology,2018, 38(4): 383-390.
[18]YAN C, CHEN W, ZHAO Z H, et al. A Probability Prediction Model of Erosion Rate for Ti-6Al-4V on High-Speed Sand Erosion[J]. Powder Technology, 2020, 364:373-381.
[19]GUO H, ZHANG C, HE Y, et al. Study on Erosion Behavior of Laser Wire Feeding Cladding High-Manganese Steel Coatings[J]. Materials, 2023, 16(17): 5733.
[20]WANG Y F, YANG Z G. Finite Element Model of Erosive Wear on Ductile and Brittle Materials[J]. Wear, 2008,265(5/6): 871-878.
[21]JOHNSON G R, COOK W. A Constitutive Model and Data for Metals Subjected to Large Strains, High Strain Rates and High Temperatures[J]. Engineering Fracture Mechanics, 1983, 21:541-548.
[22]WU H B, ZHANG S J. 3D FEM Simulation of Milling Process for Titanium Alloy Ti6Al4V[J]. The International Journal of Advanced Manufacturing Technology, 2014,71(5): 1319-1326.
[23]HADAVI V, MORENO C E, PAPINI M. Numerical and Experimental Analysis of Particle Fracture during Solid Particle Erosion, Part Ⅱ : Effect of Incident Angle, Velocity and Abrasive Size[J]. Wear, 2016, 356: 146-157.
相關鏈接